Floor installing structure for compartment
A technology for installing structures and floors, which is applied to superstructures, subassemblies of superstructures, railway car bodies, etc., and can solve problems such as difficult installation, single installation method, and prone to staggered floors
- Summary
- Abstract
- Description
- Claims
- Application Information
AI Technical Summary
Problems solved by technology
Method used
Image
Examples
Embodiment Construction
[0015] The floor mounting structure for the vehicle compartment of the present invention will be further described in detail below in conjunction with the accompanying drawings and specific embodiments.
[0016] As shown in the figure, the car floor installation structure of the present invention includes a support base body 2 formed by interconnecting support frames 1 arranged vertically and horizontally, and a floor structure layer 3 arranged above the support base body 2. As can be seen from the figure, the support frame 1 After being connected with each other, the whole supporting body of a frame structure is formed. The said floor structure layer 3 includes a honeycomb aluminum alloy profile 8, an upper glass fiber layer 9 compounded on the upper layer of the aluminum alloy profile 8, and the surface of the upper glass fiber layer is set The non-woven fabric layer 11 and the lower glass fiber layer 10 that are compositely set on the lower layer of the aluminum alloy profil...
PUM
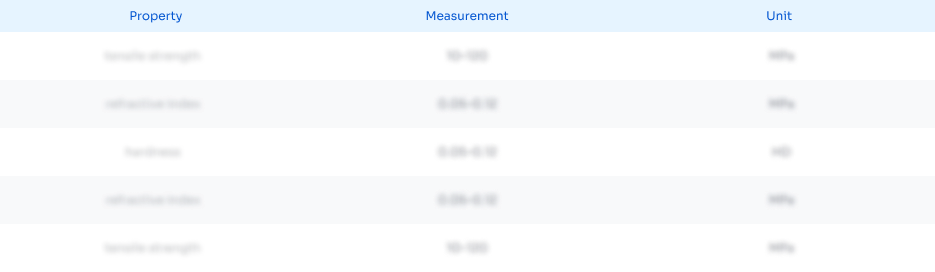
Abstract
Description
Claims
Application Information

- Generate Ideas
- Intellectual Property
- Life Sciences
- Materials
- Tech Scout
- Unparalleled Data Quality
- Higher Quality Content
- 60% Fewer Hallucinations
Browse by: Latest US Patents, China's latest patents, Technical Efficacy Thesaurus, Application Domain, Technology Topic, Popular Technical Reports.
© 2025 PatSnap. All rights reserved.Legal|Privacy policy|Modern Slavery Act Transparency Statement|Sitemap|About US| Contact US: help@patsnap.com