H-shaped motion platform modeling method based on Lagrangian dynamics
A motion platform and modeling method technology, applied in the field of dynamic modeling, can solve the problems of difficult to improve the controller control accuracy, difficult to achieve, unrealistic and so on
- Summary
- Abstract
- Description
- Claims
- Application Information
AI Technical Summary
Problems solved by technology
Method used
Image
Examples
Embodiment 1
[0064] The structure of the H-type precision motion platform is as follows: figure 1 As shown, the Y-axis is a single-axis parallel system driven by dual linear motors, and the X-axis is coupled to the dual linear motors by a permanent magnet linear motor through a beam. Therefore, the H-type motion platform can be regarded as a A structure-coupled three-degree-of-freedom servo system. The H-type motion platform can be represented by two sets of coordinates, the first set consists of the data acquisition system (y 1 the y 2 x), the second group is equivalent coordinates (YθX), where y 1 ,y 2 and x are the position output of Y1-axis, Y2-axis and X-axis respectively; Y and θ are the beam center position and deflection angle respectively; X is the position output of X-axis, that is, X=x; c g1 ,c g2 and c x Respectively, the viscous friction coefficient of each axis; c b1 and c b2 is the torsional viscous damping coefficient due to beam deflection; k b1 and k b2 is the s...
PUM
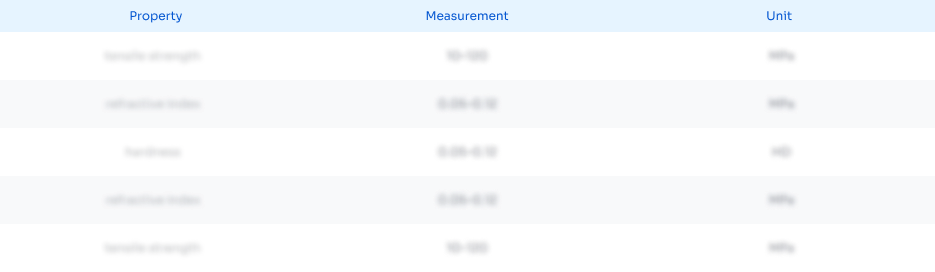
Abstract
Description
Claims
Application Information

- R&D
- Intellectual Property
- Life Sciences
- Materials
- Tech Scout
- Unparalleled Data Quality
- Higher Quality Content
- 60% Fewer Hallucinations
Browse by: Latest US Patents, China's latest patents, Technical Efficacy Thesaurus, Application Domain, Technology Topic, Popular Technical Reports.
© 2025 PatSnap. All rights reserved.Legal|Privacy policy|Modern Slavery Act Transparency Statement|Sitemap|About US| Contact US: help@patsnap.com