Method for realizing zero point calibration in laser self-calibration
A zero-point calibration and self-calibration technology, applied in the direction of using optical devices, measuring devices, instruments, etc., can solve the problem that the actual position of the laser target point deviates from the expected position.
- Summary
- Abstract
- Description
- Claims
- Application Information
AI Technical Summary
Problems solved by technology
Method used
Examples
Embodiment 1
[0023] A method for laser self-calibration to achieve zero point calibration. The laser tracking length measuring instrument is a single-frequency laser interferometer installed on the center of the mechanism with two mutually perpendicular rotation degrees of freedom. The reflective target of the tracker is an internally installed The sphere of the pyramid reflector, the apex of the pyramid coincides with the center of the sphere, the laser tracker can track the target moving in space and measure the polar coordinates of the center of the target in the polar coordinate system where the center of rotation of the tracker is the origin, that is, the origin The distance to the center of the target and the two orientation angles of the line connecting the two points.
Embodiment 2
[0025] A method for laser self-calibration to achieve zero point calibration, comprising the following steps:
[0026] a. Measure the position of the hinge point on the moving platform. Fix a rod of the parallel machine tool so that it neither stretches nor rotates around any axis, that is, fixes the position of the hinge point of the rod on the moving platform in space. Put the measuring platform in front of the moving platform, and install the laser tracker on one of the positioning holes. Place three target mirrors on the measuring moving platform, and set one of them as target mirror A. Make the moving platform move to a certain position and stay still, and use the laser tracker to detect the distances of the three target mirrors on the three positioning holes respectively. From the obtained data, the measurement coordinates of the midpoints of the three target mirrors on the moving platform can be calculated. coordinates in the system. Repeat the above process several ...
PUM
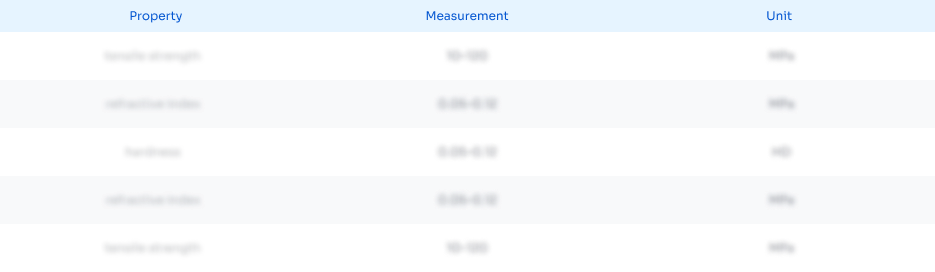
Abstract
Description
Claims
Application Information

- Generate Ideas
- Intellectual Property
- Life Sciences
- Materials
- Tech Scout
- Unparalleled Data Quality
- Higher Quality Content
- 60% Fewer Hallucinations
Browse by: Latest US Patents, China's latest patents, Technical Efficacy Thesaurus, Application Domain, Technology Topic, Popular Technical Reports.
© 2025 PatSnap. All rights reserved.Legal|Privacy policy|Modern Slavery Act Transparency Statement|Sitemap|About US| Contact US: help@patsnap.com