Low-temperature composite material storage box damage online identification method based on coupling electromechanical impedance
A technology of electromechanical impedance and composite materials, applied in the direction of material impedance, etc., can solve the problems of few applications, distortion of damage identification results, performance degradation of sensors and adhesives, etc.
- Summary
- Abstract
- Description
- Claims
- Application Information
AI Technical Summary
Problems solved by technology
Method used
Image
Examples
Embodiment
[0029] Such as Figure 2-Figure 5 The specific embodiment of the method disclosed by the invention comprises the following steps:
[0030] 1. Install a piezoelectric chip sensor on the surface of the composite laminate, and the sensor is connected to the impedance analyzer through a signal conversion switch;
[0031] 2. Install the test piece in the fixture;
[0032] 3. Use liquid nitrogen to create a low-temperature environment, and place the fixture in a low-temperature environment;
[0033] 4. The bending load is loaded in the middle section of the specimen, and the load continues to increase;
[0034] 5. Acquire the reference impedance signal, name it ImB and store it in the impedance signal space, and extract the signal characteristics such as the peak value of the real part, the slope of the imaginary part, and the frequency response of the real part, and name it MrB, SlB and FrB respectively, and store them in the Real part peak space, imaginary part slope space and ...
PUM
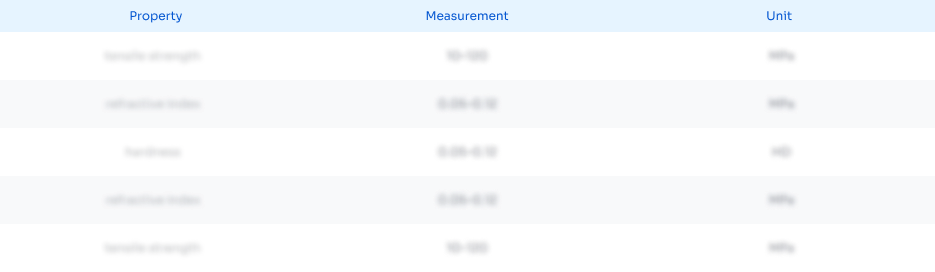
Abstract
Description
Claims
Application Information

- R&D Engineer
- R&D Manager
- IP Professional
- Industry Leading Data Capabilities
- Powerful AI technology
- Patent DNA Extraction
Browse by: Latest US Patents, China's latest patents, Technical Efficacy Thesaurus, Application Domain, Technology Topic, Popular Technical Reports.
© 2024 PatSnap. All rights reserved.Legal|Privacy policy|Modern Slavery Act Transparency Statement|Sitemap|About US| Contact US: help@patsnap.com