Decoupling mechanism for two-axis synchronous vibration test and test device
A synchronous vibration and decoupling technology, which is applied in vibration testing, measuring devices, testing of machine/structural components, etc., can solve problems such as poor safety and reliability of synchronous vibration testing devices, fatigue failure of pin rods, etc., and shorten the time for installation and commissioning , reduce rotation jamming and avoid fatigue failure
- Summary
- Abstract
- Description
- Claims
- Application Information
AI Technical Summary
Problems solved by technology
Method used
Image
Examples
Embodiment 1
[0038] This embodiment provides a decoupling mechanism for two-axis synchronous vibration test, see Figure 3 to Figure 9 , Including a hinged connecting rod 6 and a sliding component. The two ends of the hinged connecting rod 6 are hinged to the horizontal vibration generator 2 and the worktable 3 respectively. The sliding component is connected to the vertical vibration generator and the worktable 3 respectively. The hinged connecting rod 6 can When rotating in the vertical direction, the sliding direction of the sliding assembly is parallel to the vibration direction of the horizontal vibration generator 2.
[0039] In practical applications, when the worktable 3 vibrates vertically under the action of the vertical vibration generator 1, the hinged link 6 rotates relative to the worktable 3 through force transmission, thereby compensating for the vertical vibration. At the same time, when the worktable 3 is horizontally vibrated under the action of the horizontal vibration gene...
Embodiment 2
[0056] This embodiment provides a two-axis synchronous vibration test device, see Figure 10 to Figure 11 , Including the workbench 3, the horizontal vibration generator 2, the vertical vibration generator 1 and the decoupling mechanism provided in the first embodiment, the workbench 3, the horizontal vibration generator 2 and the vertical vibration generator 1 are all set on the base 12 on.
[0057] Compared with the prior art, the beneficial effects of the two-axis synchronous vibration test device provided in this embodiment are basically the same as those of the decoupling mechanism provided in the first embodiment, which will not be repeated here.
PUM
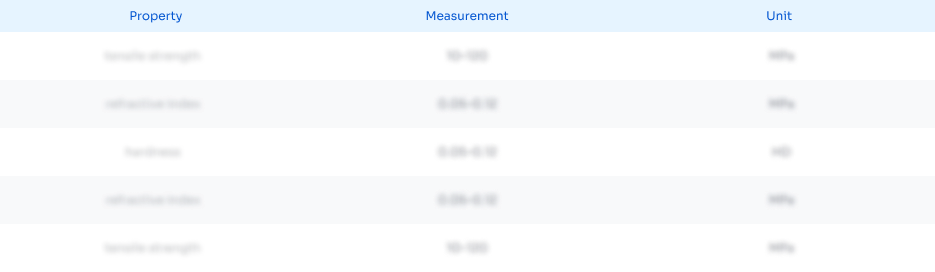
Abstract
Description
Claims
Application Information

- R&D
- Intellectual Property
- Life Sciences
- Materials
- Tech Scout
- Unparalleled Data Quality
- Higher Quality Content
- 60% Fewer Hallucinations
Browse by: Latest US Patents, China's latest patents, Technical Efficacy Thesaurus, Application Domain, Technology Topic, Popular Technical Reports.
© 2025 PatSnap. All rights reserved.Legal|Privacy policy|Modern Slavery Act Transparency Statement|Sitemap|About US| Contact US: help@patsnap.com