Support device for aircraft tail and fuselage connection strength test
A connection strength and support device technology, which is applied in the field of aircraft vertical tail and fuselage connection strength test device, can solve the problems of high cost, great influence on the mechanical performance of the vertical tail, and difficulty in realizing it, and achieve the effect of reducing risks
- Summary
- Abstract
- Description
- Claims
- Application Information
AI Technical Summary
Problems solved by technology
Method used
Image
Examples
Embodiment Construction
[0043] It should be noted that, in the case of no conflict, the embodiments of the present invention and the features in the embodiments can be combined with each other.
[0044] The present invention will be described in detail below with reference to the accompanying drawings and examples.
[0045] Such as Figure 1-Figure 8As shown, a support device used for the strength test of the connection between the vertical tail and the fuselage of an aircraft includes two groups of rod systems arranged symmetrically, and each group of rod systems includes a front rod system a, a middle front rod system b, a middle Rear rod system c and rear rod system d, the arrangement of the front rod system a, the middle front rod system b, the middle rear rod system c and the rear rod system d of the two groups of rod systems is in line with the position of the joint of the vertical tail of the aircraft Correspondingly, the front rod system a, the middle front rod system b, the middle rear rod ...
PUM
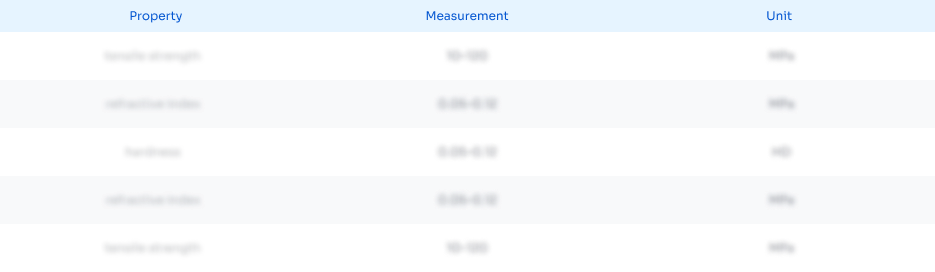
Abstract
Description
Claims
Application Information

- R&D
- Intellectual Property
- Life Sciences
- Materials
- Tech Scout
- Unparalleled Data Quality
- Higher Quality Content
- 60% Fewer Hallucinations
Browse by: Latest US Patents, China's latest patents, Technical Efficacy Thesaurus, Application Domain, Technology Topic, Popular Technical Reports.
© 2025 PatSnap. All rights reserved.Legal|Privacy policy|Modern Slavery Act Transparency Statement|Sitemap|About US| Contact US: help@patsnap.com