Milling machine control system and control method
A control system and control method technology, applied in the field of construction machinery, can solve the problems of laxity, scraper deformation, jitter, etc.
- Summary
- Abstract
- Description
- Claims
- Application Information
AI Technical Summary
Problems solved by technology
Method used
Image
Examples
Embodiment Construction
[0027] The technical solutions of the present invention will be further described below in conjunction with the accompanying drawings and embodiments. It should be understood that the specific embodiments described here are only used to explain the present invention, but not to limit the present invention. In addition, it should be noted that, for the convenience of description, only the parts related to the present invention are shown in the drawings but not all of them.
[0028] The present invention provides a control system of a milling machine, the control system is mainly used to control the scraper 3 and the feeding device 4 in the milling machine, such as figure 1 and figure 2 As shown, the scraper 3 is slidingly connected to the milling bin 2 at the rear of the fuselage 1, one end of the feeding device 4 is hinged to the scraper 3, and the other end of the feeding device 4 extends obliquely upward in a direction away from the scraper 3, The material conveying belt ...
PUM
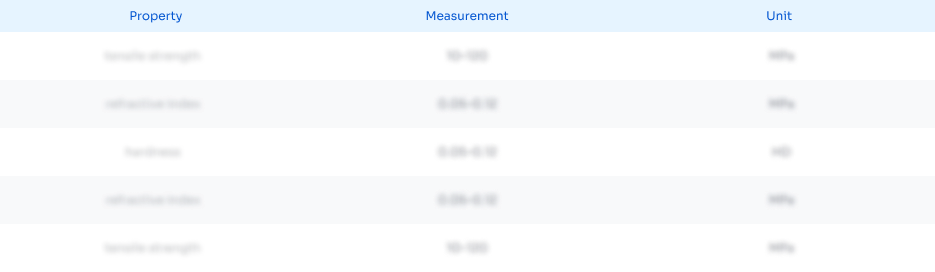
Abstract
Description
Claims
Application Information

- R&D Engineer
- R&D Manager
- IP Professional
- Industry Leading Data Capabilities
- Powerful AI technology
- Patent DNA Extraction
Browse by: Latest US Patents, China's latest patents, Technical Efficacy Thesaurus, Application Domain, Technology Topic, Popular Technical Reports.
© 2024 PatSnap. All rights reserved.Legal|Privacy policy|Modern Slavery Act Transparency Statement|Sitemap|About US| Contact US: help@patsnap.com