A torsional quasi-zero stiffness vibration isolator with adjustable negative stiffness and its control method
A quasi-zero stiffness, vibration isolator technology, applied in the direction of rotation vibration suppression, spring/shock absorber functional characteristics, spring/shock absorber design characteristics, etc., can solve problems such as difficult miniaturization, poor controllability, and complex structure , to achieve low dynamic stiffness, compact structure, and broaden the effect of vibration isolation frequency band
- Summary
- Abstract
- Description
- Claims
- Application Information
AI Technical Summary
Problems solved by technology
Method used
Image
Examples
Embodiment Construction
[0016] The present invention will be described in further detail below in conjunction with the accompanying drawings and specific embodiments.
[0017] like figure 1 As shown, a torsional quasi-zero stiffness vibration isolator with adjustable negative stiffness in the present invention includes a front shell 1, a rear shell 2 and a permanent magnet excitation mechanism inside the cavity. Wherein the front shell 1 and the rear shell 2 are fixedly connected by bolts and nuts. The inside of the front housing 1 and the rear housing 2 has a boss along the axial direction, which cooperates with the groove of the annular permanent magnet clamping mechanism 8 inside the permanent magnet excitation mechanism to prevent the permanent magnet excitation mechanism from generating a gap relative to the front housing 1 and the rear housing 2. Rotational movement. Gaskets 3 are installed at the front and rear sides of the permanent magnet excitation mechanism in contact with the front casi...
PUM
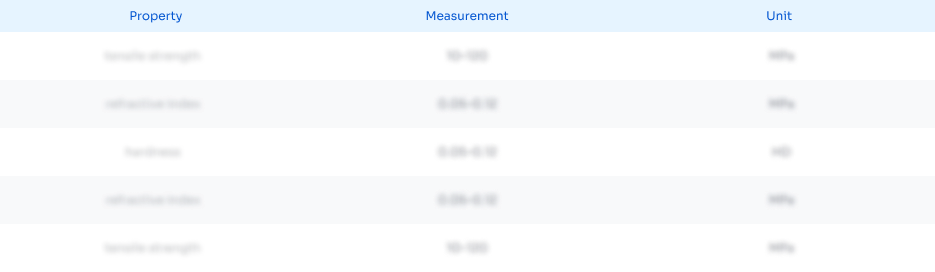
Abstract
Description
Claims
Application Information

- Generate Ideas
- Intellectual Property
- Life Sciences
- Materials
- Tech Scout
- Unparalleled Data Quality
- Higher Quality Content
- 60% Fewer Hallucinations
Browse by: Latest US Patents, China's latest patents, Technical Efficacy Thesaurus, Application Domain, Technology Topic, Popular Technical Reports.
© 2025 PatSnap. All rights reserved.Legal|Privacy policy|Modern Slavery Act Transparency Statement|Sitemap|About US| Contact US: help@patsnap.com