Preparation method of modified polysiloxane/polymethyl methacrylate composite material
A technology of polymethyl methacrylate and methyl methacrylate is applied in the field of composite materials, which can solve the problems that optical materials cannot achieve light transmittance and haze, and achieve the effect of avoiding uneven dispersion.
- Summary
- Abstract
- Description
- Claims
- Application Information
AI Technical Summary
Problems solved by technology
Method used
Image
Examples
Embodiment 1
[0032] (1) Preparation of hydroxy-terminated polysiloxane: react 30mL octamethylcyclotetrasiloxane, 24mL toluene and 6g KOH at 120°C for 6h, the stirring speed during the reaction is 150r / min, and cool down to 60°C , with a mass fraction of 15% H 2 SO 4 Neutralize the reaction solution to a pH value of 7, stir for 2 hours, then separate the liquids, take the target liquid in the upper layer, and evaporate toluene to obtain hydroxyl-terminated polysiloxane;
[0033] (2) Preparation of modified polysiloxane: Mix 20 mL of hydroxyl-terminated polysiloxane prepared in step (1) with 20 mL of dichloromethane, add 0.2 g of anhydrous Na 2 CO 3 , placed in ice water, dropwise added a mixture of 10mL dichloromethane and 4mL methacryloyl chloride at a rate of 8 drops / min, after the dropwise addition was completed, warmed up to room temperature and continued to react for 2h, followed by 5% NaHCO 3 Solution, saturated saline and deionized water were washed twice, the liquid was separated...
Embodiment 2
[0036] (1) Preparation of hydroxyl-terminated polysiloxane: react 30mL octamethylcyclotetrasiloxane, 24mL toluene and 6g KOH at 135°C for 4h, the stirring speed during the reaction is 130r / min, and cool down to 60°C , with a mass fraction of 15% H 2 SO 4 Neutralize the reaction solution to a pH value of 7, stir for 3 hours, then separate the liquids, take the target liquid in the upper layer, and evaporate toluene to obtain hydroxyl-terminated polysiloxane;
[0037] (2) Preparation of modified polysiloxane: Mix 20 mL of hydroxyl-terminated polysiloxane prepared in step (1) with 20 mL of dichloromethane, add 0.2 g of anhydrous Na 2 CO 3 , placed in ice water, dropwise added a mixture of 10mL dichloromethane and 3mL acryloyl chloride at a rate of 10 drops / min, after the dropwise addition, warmed up to room temperature and continued to react for 1h, followed by 5% NaHCO 3 Solution, saturated saline and deionized water were washed twice, separated, the temperature of the target...
Embodiment 3
[0040] (1) Preparation of hydroxyl-terminated polysiloxane: react 30mL octamethylcyclotetrasiloxane, 24mL toluene and 6g KOH at 130°C for 5h, the stirring speed during the reaction is 120r / min, and cool down to 60°C , with a mass fraction of 15% H 2 SO 4 Neutralize the reaction solution to a pH value of 7, stir for 3 hours, then separate the liquids, take the target liquid in the upper layer, and evaporate toluene to obtain hydroxyl-terminated polysiloxane;
[0041] (2) Preparation of modified polysiloxane: Mix 20 mL of hydroxyl-terminated polysiloxane prepared in step (1) with 20 mL of dichloromethane, add 0.2 g of anhydrous Na 2 CO 3 , placed in ice water, dropwise added a mixture of 10mL dichloromethane and 3.5mL acryloyl chloride at a rate of 12 drops / min, after the dropwise addition was completed, warmed up to room temperature and continued to react for 2 hours, followed by 5% NaHCO 3 Solution, saturated saline and deionized water were washed twice, separated, the temp...
PUM
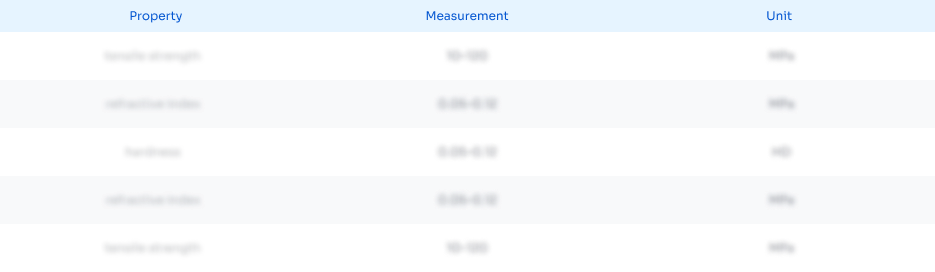
Abstract
Description
Claims
Application Information

- Generate Ideas
- Intellectual Property
- Life Sciences
- Materials
- Tech Scout
- Unparalleled Data Quality
- Higher Quality Content
- 60% Fewer Hallucinations
Browse by: Latest US Patents, China's latest patents, Technical Efficacy Thesaurus, Application Domain, Technology Topic, Popular Technical Reports.
© 2025 PatSnap. All rights reserved.Legal|Privacy policy|Modern Slavery Act Transparency Statement|Sitemap|About US| Contact US: help@patsnap.com