Production process for refining secondary brine by replacing sun-dried sea salt with well and rock salt
A secondary brine and production process technology, applied in the chlor-alkali industry, can solve the problems of aluminum ions and other impurities exceeding the standard, and achieve the effects of reducing the amount of solid waste salt mud, reducing the salt consumption per ton of alkali, and reducing the opening frequency
- Summary
- Abstract
- Description
- Claims
- Application Information
AI Technical Summary
Problems solved by technology
Method used
Image
Examples
Embodiment 1
[0042] After fully using well mine salt instead of sun-dried sea salt, the Si content in the secondary brine is 10-20ppm, Al 3+ Content 120~160ppb, Si content and Al 3+ content exceeded the standard.
Embodiment 2
[0044] When 10% sea salt is mixed into well mine salt, Si content in secondary brine is 5-12ppm, Al 3+ Content 55~120ppb, Al 3+ The content exceeds the standard.
Embodiment 3
[0046] When the amount of sea salt mixed in well mine salt reaches 25%, Si content in secondary brine is less than 2.3ppm, Al 3+ Content3+ The content does not exceed the standard.
[0047] After using well mine salt instead of sea salt, the cleaning of the salt pond was extended from the original semi-annual cleaning to every two years, and the salt consumption per ton of alkali was greatly reduced, from 1.6t salt / ton alkali (folded) to 1.51t salt / ton alkali (100 percent); consumption of auxiliary materials FeCl 3 Reduced from 0.3t / ton of alkali (reduced to 100) to 0.05t / ton of alkali (reduced to 100%; consumption of auxiliary material NaOH was reduced from 30kg / ton of alkali (reduced to 100%) to 20kg / ton of alkali (reduced to 100%), consumption of auxiliary material NaCO 3 Reduced from 9kg / ton of alkali (100%) to 6kg / ton of alkali (100%); the frequency of opening the denitrification system was reduced, and the operation was from 8000h / year to 2900h / year; the amount of solid...
PUM
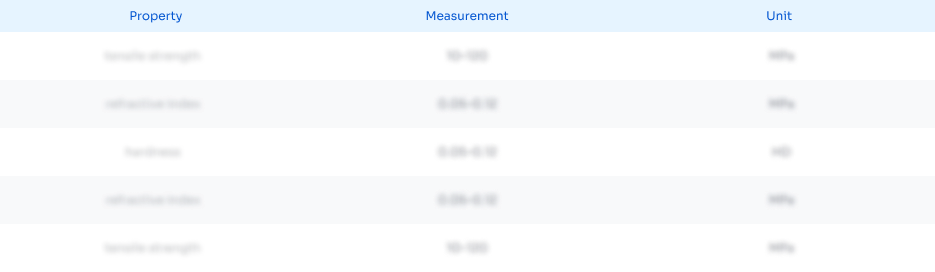
Abstract
Description
Claims
Application Information

- R&D
- Intellectual Property
- Life Sciences
- Materials
- Tech Scout
- Unparalleled Data Quality
- Higher Quality Content
- 60% Fewer Hallucinations
Browse by: Latest US Patents, China's latest patents, Technical Efficacy Thesaurus, Application Domain, Technology Topic, Popular Technical Reports.
© 2025 PatSnap. All rights reserved.Legal|Privacy policy|Modern Slavery Act Transparency Statement|Sitemap|About US| Contact US: help@patsnap.com