Stacking robot and using method thereof
A palletizing robot and balancer technology, applied in the field of palletizing robots, can solve the problems of high manufacturing and processing costs, heavy balancing devices, complex mechanical structures, etc., and achieve the effects of reducing labor intensity, simple structure of mechanical arms, and small size
- Summary
- Abstract
- Description
- Claims
- Application Information
AI Technical Summary
Problems solved by technology
Method used
Image
Examples
Embodiment Construction
[0062] Below in conjunction with accompanying drawing, the present invention is described in further detail:
[0063] Such as Figure 1-1 to Figure 4C As shown, the present invention is a palletizing robot 10, comprising a support base 11, a waist seat mechanism 12, a mechanical swing arm mechanism 13A, a mechanical swing arm mechanism 13B, a balancer 14, a link mechanism 15, a wrist assembly mechanism 16, a Lan Pan17.
[0064] The waist seat mechanism 12 is connected to the support seat 11 through a rotating pair to form a component capable of rotating around a specified rotation axis; the mechanical swing arm mechanism 13A is connected to the waist seat mechanism 12 to be able to rotate around a specified rotation axis; The balancer 14 is connected with the waist seat mechanism 12 and the mechanical swing arm mechanism 13A respectively; the mechanical swing arm mechanism 13B is connected with the mechanical swing arm mechanism 13A and the wrist assembly mechanism 16 respect...
PUM
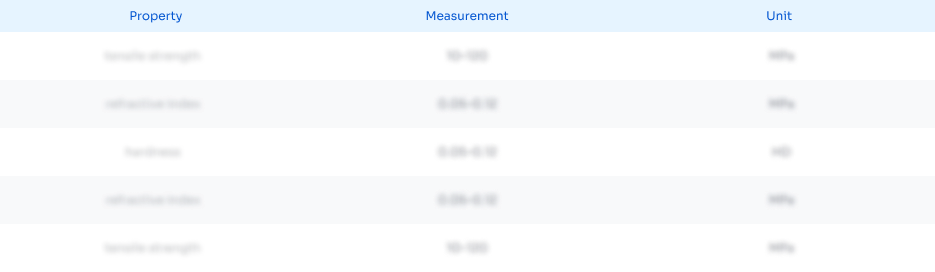
Abstract
Description
Claims
Application Information

- R&D Engineer
- R&D Manager
- IP Professional
- Industry Leading Data Capabilities
- Powerful AI technology
- Patent DNA Extraction
Browse by: Latest US Patents, China's latest patents, Technical Efficacy Thesaurus, Application Domain, Technology Topic, Popular Technical Reports.
© 2024 PatSnap. All rights reserved.Legal|Privacy policy|Modern Slavery Act Transparency Statement|Sitemap|About US| Contact US: help@patsnap.com