Bearing drive mechanism for vehicle door system
A driving mechanism and vehicle door technology, applied in the field of rail transit doors, can solve the problems of inability to judge the locked or open state, limit the bearing capacity of the bearing driving mechanism, and require high precision of parts, so as to facilitate installation, debugging and maintenance, and improve rigidity. and the effect of carrying capacity, assuring stability and safety
- Summary
- Abstract
- Description
- Claims
- Application Information
AI Technical Summary
Problems solved by technology
Method used
Image
Examples
Embodiment Construction
[0016] like figure 1 , the fixed frame 1 is fixed on the vehicle, the fixed frame 1 is fixedly connected with the slideway 2, and there is a drive assembly 4 used to drive the doors on both sides on the bearing transverse bracket 3, and the drive assembly 4 includes a screw rod 403, a drive motor 401 and a door control The device 402 is divided into a right locking slideway 5 and a left locking slideway 6 on both sides of the carrying horizontal bracket 3, the fixed frame 1 is fixedly connected with the left locking slideway 5 and the right locking slideway 6, and the carrying horizontal bracket 3 There is a locking mechanism 7 in the middle, the left nut assembly 8 is connected with the left sliding cylinder 10 through the linkage frame 19, the right nut assembly 9 is connected with the right sliding cylinder 11 through the linkage frame 19, the left sliding cylinder 10 is fixedly connected with the left door leaf, and the right The sliding cylinder 11 is fixedly connected wi...
PUM
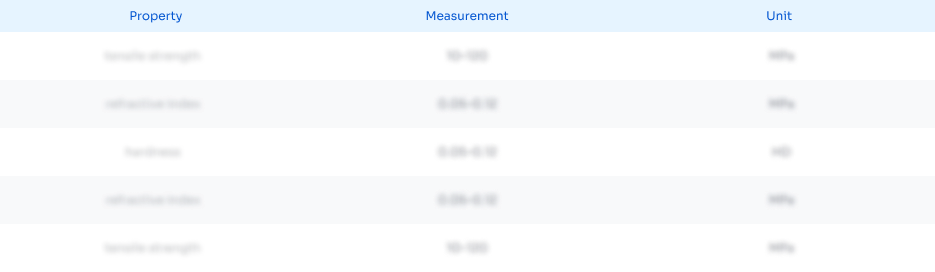
Abstract
Description
Claims
Application Information

- R&D
- Intellectual Property
- Life Sciences
- Materials
- Tech Scout
- Unparalleled Data Quality
- Higher Quality Content
- 60% Fewer Hallucinations
Browse by: Latest US Patents, China's latest patents, Technical Efficacy Thesaurus, Application Domain, Technology Topic, Popular Technical Reports.
© 2025 PatSnap. All rights reserved.Legal|Privacy policy|Modern Slavery Act Transparency Statement|Sitemap|About US| Contact US: help@patsnap.com