Automatic ammunition feeding and ramming failure on-line monitoring and prediction method
A prediction method and technology for ammunition supply and delivery, which can be applied to ammunition supply, weapon accessories, offensive equipment, etc., can solve the problems of large error in results, large vibration signal noise interference, and difficulty in establishing vibration signals, so as to achieve precise fault detection and resolution , Solve low efficiency and improve maintenance efficiency
- Summary
- Abstract
- Description
- Claims
- Application Information
AI Technical Summary
Problems solved by technology
Method used
Image
Examples
Embodiment Construction
[0029] Now in conjunction with embodiment, accompanying drawing, the present invention will be further described:
[0030] The common failure forms of the artillery ammunition supply and delivery mechanical system are mainly failures such as untimely supply of ammunition, jamming during the supply and delivery process, and insufficient delivery of ammunition. The study found that the core components and causes affecting the failure of the bomb supply and delivery are as follows:
[0031] During the feeding process, the projectile is driven by the bomb feeding chain, and the bomb feeding chain is powered by the chain driven by the sprocket. Due to the inevitable friction between the sprocket and the roller, the sprocket and the roller wear to a certain extent, resulting in a certain degree of wear during the feeding process. The speed and stability of the ammunition are affected, resulting in failures such as the supply and delivery of the ammunition being stuck or the delivery...
PUM
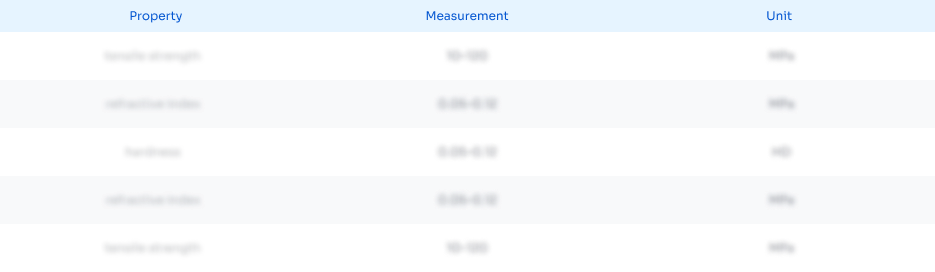
Abstract
Description
Claims
Application Information

- Generate Ideas
- Intellectual Property
- Life Sciences
- Materials
- Tech Scout
- Unparalleled Data Quality
- Higher Quality Content
- 60% Fewer Hallucinations
Browse by: Latest US Patents, China's latest patents, Technical Efficacy Thesaurus, Application Domain, Technology Topic, Popular Technical Reports.
© 2025 PatSnap. All rights reserved.Legal|Privacy policy|Modern Slavery Act Transparency Statement|Sitemap|About US| Contact US: help@patsnap.com