Compound polyurethane sleeper pad and preparation method thereof
A composite polyurethane technology, applied in the direction of track, ballast layer, building, etc., can solve the problems of railway ballast gravel pulverization, low strength of sleeper pads, piercing of sleeper pads, etc. The effect of tamping cycle and delaying compaction time
- Summary
- Abstract
- Description
- Claims
- Application Information
AI Technical Summary
Problems solved by technology
Method used
Image
Examples
preparation example Construction
[0036] The method for preparing the composite polyurethane sleeper pad specifically includes the following steps:
[0037] A. Lay a layer of non-woven fabric on a flat workbench with side guards.
[0038] B. The polyurethane composite material and reinforcing fibers are poured uniformly through a casting machine with fiber cutting and adding functions to form a casting material.
[0039] The method for preparing the polyurethane composition is as follows: First, sequentially add polyether polyol a, polyether polyol b, polyether polyol c, blowing agent, catalyst and auxiliary agent into the mixing and stirring tank, stirring for 60 minutes, and filling Sealed preservation, formulated into component A; take the modified product of diphenylmethane diisocyanate or polyphenyl polymethylene polyisocyanate as component B; put component A and component B into fiber cutting and The silo of the functional polyurethane casting machine is ready to be used, and the polyurethane composite materia...
Embodiment 1
[0043] This embodiment provides a composite polyurethane sleeper pad, which includes a composite polyurethane layer composed of a blend of polyurethane composite materials and reinforcing fibers and a non-woven fabric layer 3, the non-woven fabric layer being located below the composite polyurethane layer.
[0044] The raw materials required to prepare the sleeper pad of this embodiment are: the non-woven fabric layer is 200g dotted polyamide 6 non-woven fabric, and the total mass of the reinforcing fiber is 10%, the diameter is 10um, and the length is 2mm. The total mass of the castable is 90% polyurethane composition; the polyurethane composition includes 16 parts of Jiahua Chemical’s polyether polyol 303, 23 parts of BASF’s PTHF1000, 23.04 parts of Bluestar Dongda’s HPOP40, 0.2 parts Deionized water, 0.01 parts of catalyst dibutyl tin dilaurate, 0.05 parts of catalyst triethylene diamine, 1 part of Mesode Chemical’s foam stabilizer AK8805, 0.3 part of UV absorber UV327, 0.4 par...
Embodiment 2
[0047] The difference in the structure of the composite polyurethane sleeper pad between this embodiment and the embodiment 1 lies in the fact that this embodiment is provided with a skeleton on the top of the composite polyurethane layer formed by blending polyurethane composite materials and reinforcing fibers, and the skeleton is a polyurethane skeleton.
[0048] The raw materials needed to prepare the sleeper pad of this embodiment are: the non-woven fabric layer is selected from the point-patterned polyamide 6 non-woven fabric with a weight of 200g, the total mass of the reinforcing fiber is 18%, the diameter is 12um, and the length is 3mm. The total mass of the castable is 82% polyurethane composition; the polyurethane composition includes 11 parts of triethanolamine, 25 parts of BASF’s PTHF1000, 21.12 parts of Bluestar Dongda’s HPOP40, 0.1 parts of deionized water, and 0.05 parts of catalyst Dibutyltin dilaurate, 0.1 parts of catalyst triethylenediamine, 2 parts of Mesode C...
PUM
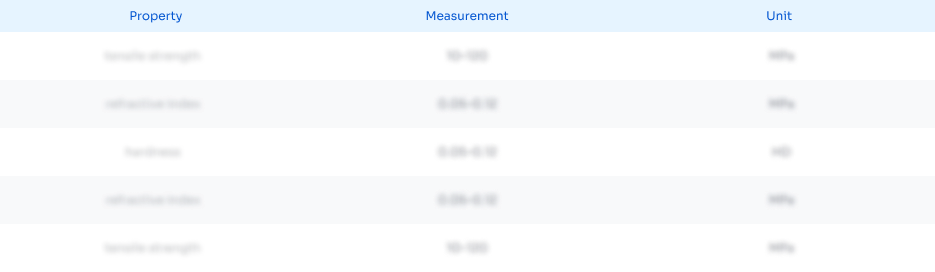
Abstract
Description
Claims
Application Information

- R&D
- Intellectual Property
- Life Sciences
- Materials
- Tech Scout
- Unparalleled Data Quality
- Higher Quality Content
- 60% Fewer Hallucinations
Browse by: Latest US Patents, China's latest patents, Technical Efficacy Thesaurus, Application Domain, Technology Topic, Popular Technical Reports.
© 2025 PatSnap. All rights reserved.Legal|Privacy policy|Modern Slavery Act Transparency Statement|Sitemap|About US| Contact US: help@patsnap.com