Oilproof sole material and preparation method thereof
A shoe sole material and oil-proof technology, which is applied in shoe soles, footwear, applications, etc., can solve problems such as degummed soles, rubber swelling, and molecular structure destruction, and achieve improved comfort, oil-proof performance, good elasticity, and good oil resistance effect of effect
- Summary
- Abstract
- Description
- Claims
- Application Information
AI Technical Summary
Problems solved by technology
Method used
Image
Examples
Embodiment 1
[0034] An oil-proof shoe sole material and a preparation method thereof, comprising the following raw materials in parts by weight:
[0035] APAO resin, 35 parts;
[0036] APP resin, 20 parts;
[0037] Nitrile rubber, 5 parts;
[0038] fiberglass, 20 parts
[0039] calcium carbonate, 6 parts;
[0040] Calcium stearate, 2 parts;
[0041] Bis(2,2,6,6-tetramethyl-4-piperidinyl) sebacate, 0.5 parts.
[0042] (3) The heat stabilizer is a mixture of calcium stearate and zinc stearate in a ratio of 1:1.
[0043] A preparation method for oil-resistant sole material, comprising the steps of:
[0044] (1) Take by weighing 35 parts of APAO resins, 20 parts of APP resins, 5 parts of nitrile rubber, 20 parts of glass fibers,
[0045] The raw materials of 6 parts of calcium carbonate, 3 parts of calcium stearate and 0.5 part of bis(2,2,6,6-tetramethyl-4-piperidinyl) sebacate are for use;
[0046] (2) Put each raw material weighed in the step (1) into a vacuum oven for drying respect...
Embodiment 2
[0050] An oil-proof shoe sole material and a preparation method thereof, comprising the following raw materials in parts by weight:
[0051] APAO resin, 40 parts;
[0052] APP resin, 25 parts;
[0053] Nitrile rubber, 7 parts;
[0054] fiberglass, 23 servings
[0055] calcium carbonate, 7 parts;
[0056] Calcium Stearate, 3 parts;
[0057] Bis(2,2,6,6-tetramethyl-4-piperidinyl) sebacate, 1 part.
[0058] (3) The heat stabilizer is a mixture of calcium stearate and zinc stearate in a ratio of 1:1.
[0059] A preparation method for oil-resistant sole material, comprising the steps of:
[0060] (1) Take by weighing 40 parts of APAO resin, 25 parts of APP resin, 7 parts of nitrile rubber, 23 parts of glass fiber,
[0061] The raw materials of 7 parts of calcium carbonate, 3 parts of calcium stearate and 1 part of bis(2,2,6,6-tetramethyl-4-piperidinyl) sebacate are for use;
[0062] (2) Put each raw material weighed in the step (1) into a vacuum oven for drying respectively...
Embodiment 3
[0066] An oil-proof shoe sole material and a preparation method thereof, comprising the following raw materials in parts by weight:
[0067] APAO resin, 45 parts;
[0068] APP resin, 27 parts;
[0069] Nitrile rubber, 10 parts;
[0070] fiberglass, 28 servings
[0071] Calcium carbonate, 10 parts;
[0072] Calcium stearate, 2 parts;
[0073] Bis(2,2,6,6-tetramethyl-4-piperidinyl) sebacate, 1.5 parts.
[0074] (3) The heat stabilizer is a mixture of calcium stearate and zinc stearate in a ratio of 1:1.
[0075] A preparation method for oil-resistant sole material, comprising the steps of:
[0076] (1) Weigh 45 parts of APAO resin, 27 parts of APP resin, 10 parts of nitrile rubber, 28 parts of glass fiber, 10 parts of calcium carbonate, 2 parts of calcium stearate and 1.5 parts of bis(2,2,6,6- The raw material of tetramethyl-4-piperidinyl) sebacate is stand-by;
[0077] (2) Put each raw material weighed in step (1) into a vacuum drying oven for drying respectively, the d...
PUM
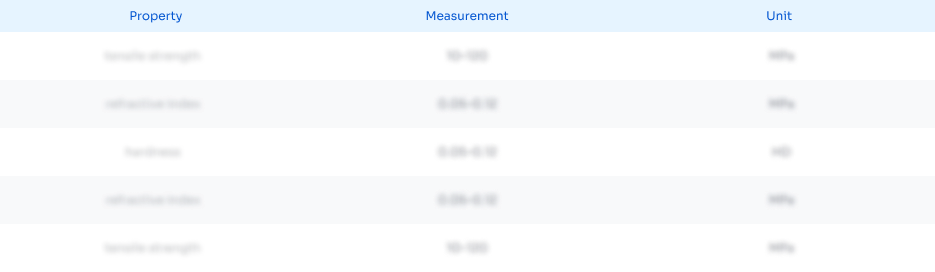
Abstract
Description
Claims
Application Information

- Generate Ideas
- Intellectual Property
- Life Sciences
- Materials
- Tech Scout
- Unparalleled Data Quality
- Higher Quality Content
- 60% Fewer Hallucinations
Browse by: Latest US Patents, China's latest patents, Technical Efficacy Thesaurus, Application Domain, Technology Topic, Popular Technical Reports.
© 2025 PatSnap. All rights reserved.Legal|Privacy policy|Modern Slavery Act Transparency Statement|Sitemap|About US| Contact US: help@patsnap.com