Material dynamic mechanical parameter acquisition device and method
A technology of dynamic mechanics and parameter acquisition, which is applied in the direction of measuring devices, analyzing materials, and testing the strength of materials by applying a stable torsion force. Wave synchronization problem, good experimental repeatability effect
- Summary
- Abstract
- Description
- Claims
- Application Information
AI Technical Summary
Problems solved by technology
Method used
Image
Examples
Embodiment 1
[0054] This embodiment provides a device for acquiring dynamic mechanical parameters of materials, which includes an electromagnetic Hopkinson tie rod loading unit, an electromagnetic Hopkinson torsion bar loading unit, and a stress wave synchronization unit. The above components will be described in detail below.
[0055] The electromagnetic Hopkinson rod loading unit includes a power supply 21, a stretching wave capacitor charger 2 and a stretching wave loading gun 3; the stretching wave capacitor charger 2 adopts the power supply part of the existing electromagnetic riveting equipment, and the stretching wave capacitor charger 2 adopts the power supply part of the existing electromagnetic riveting equipment, and The positive output line of the output of the wave capacitor charger 2 is connected with the positive line of the tensile wave loading gun 3, and the negative output line is connected with the negative line of the loading gun; the tensile wave loading gun 3 includes a...
PUM
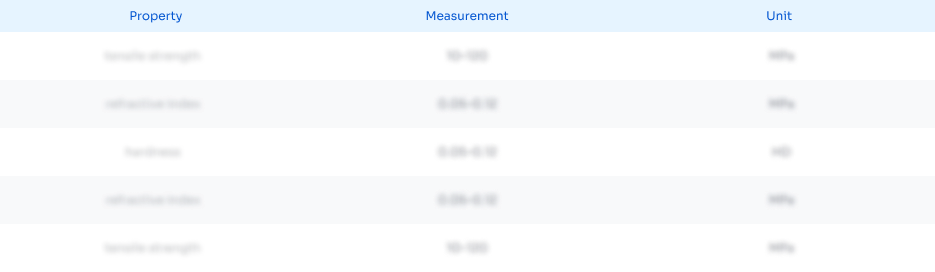
Abstract
Description
Claims
Application Information

- R&D Engineer
- R&D Manager
- IP Professional
- Industry Leading Data Capabilities
- Powerful AI technology
- Patent DNA Extraction
Browse by: Latest US Patents, China's latest patents, Technical Efficacy Thesaurus, Application Domain, Technology Topic, Popular Technical Reports.
© 2024 PatSnap. All rights reserved.Legal|Privacy policy|Modern Slavery Act Transparency Statement|Sitemap|About US| Contact US: help@patsnap.com