Method for realizing manipulator rapid grabbing control in robot stacking system
A technology of robots and manipulators, which is applied in the field of manipulator material stacking and machinery, can solve the problems of reduced production efficiency and production capacity, prolonged glass grabbing cycle, and affecting stacking efficiency, so as to improve work efficiency, speed up industrial production tempo, The effect of improving production efficiency and productivity
- Summary
- Abstract
- Description
- Claims
- Application Information
AI Technical Summary
Problems solved by technology
Method used
Image
Examples
Embodiment Construction
[0050] In order to describe the technical content of the present invention more clearly, further description will be given below in conjunction with specific embodiments.
[0051] figure 1It is a structural schematic diagram of the method for realizing the flying grasping control of the manipulator in the robot stacking system of the present invention. In this figure, the method for realizing the flying grasping control of the manipulator in the robot stacking system of the present invention is being used to grab glass 9 for glass 9 Stacking, that is, glass is the material to be stacked. In the robot stacking system, the method for realizing manipulator flying grasping control, the robot stacking system includes a robot 4, a PLC control system 7, a first photoelectric sensor 1 and a second photoelectric sensor 1, wherein the first photoelectric The sensor 1 and the second photoelectric sensor 1 are placed in parallel upstream of the roller table 2, and the middle point of the...
PUM
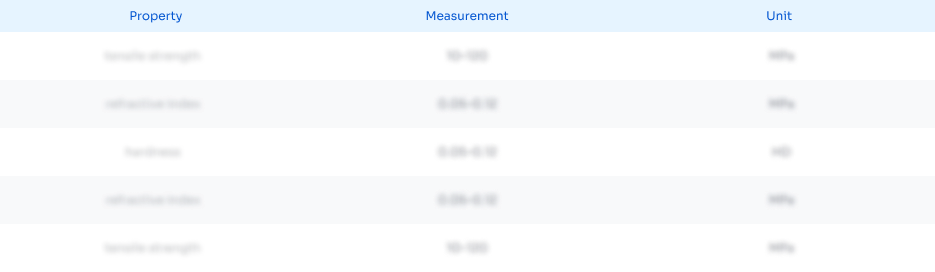
Abstract
Description
Claims
Application Information

- R&D
- Intellectual Property
- Life Sciences
- Materials
- Tech Scout
- Unparalleled Data Quality
- Higher Quality Content
- 60% Fewer Hallucinations
Browse by: Latest US Patents, China's latest patents, Technical Efficacy Thesaurus, Application Domain, Technology Topic, Popular Technical Reports.
© 2025 PatSnap. All rights reserved.Legal|Privacy policy|Modern Slavery Act Transparency Statement|Sitemap|About US| Contact US: help@patsnap.com