Motorcycle rear vehicle body structure
A rear car body and motorcycle technology, applied to steering mechanisms, bicycle accessories, axle suspension devices, etc., can solve the problems of low assembly efficiency, low strength of flat forks, and increased production costs, and achieve easy assembly and adjustment, and reduce inventory Effect of preparation and improvement of assembly efficiency
- Summary
- Abstract
- Description
- Claims
- Application Information
AI Technical Summary
Problems solved by technology
Method used
Image
Examples
Embodiment Construction
[0029] The present invention will be further described below in conjunction with embodiment and accompanying drawing.
[0030] like figure 1 and figure 2 As shown, a rear body structure of a motorcycle includes a flat fork 100 on which a rear fender 210, a chain guard 220, a chain guard 300, a rear wheel mounting shaft 400 and a rear shock absorber are assembled. 500. Among them, the rear fender 210 and the chain guard 220 are integrally formed to form the rear mudguard chain guard 200, which has an ingenious structure and high reliability. Workers only need to align once to complete the installation, and the number of fixed points for installation is reduced. The efficiency of assembly has been greatly improved and the inventory preparation of parts has been reduced. The flat fork 100 is made of aluminum alloy, and it is molded at one time through a casting process. The flat fork 100 made of aluminum alloy is light in weight and high in strength, and the flat fork 100 fo...
PUM
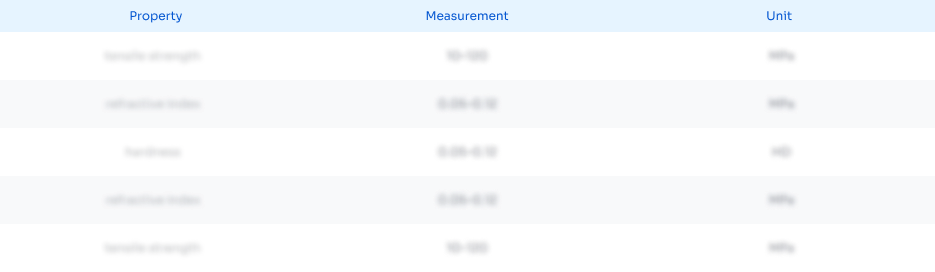
Abstract
Description
Claims
Application Information

- R&D
- Intellectual Property
- Life Sciences
- Materials
- Tech Scout
- Unparalleled Data Quality
- Higher Quality Content
- 60% Fewer Hallucinations
Browse by: Latest US Patents, China's latest patents, Technical Efficacy Thesaurus, Application Domain, Technology Topic, Popular Technical Reports.
© 2025 PatSnap. All rights reserved.Legal|Privacy policy|Modern Slavery Act Transparency Statement|Sitemap|About US| Contact US: help@patsnap.com