Collaborative task planning method of remote operating system of multiple mechanical arms based on Petri network
A task planning and operating system technology, which is applied to manipulators, program-controlled manipulators, manufacturing tools, etc., can solve the problems of large amount of calculation, high efficiency, and non-one-to-one correspondence, and achieve the effect of convenient control and improved operation efficiency
- Summary
- Abstract
- Description
- Claims
- Application Information
AI Technical Summary
Problems solved by technology
Method used
Image
Examples
specific Embodiment
[0053] Step 1: Petri net six-tuple expression structure description:
[0054] Petri net is a meshed information energy flow model, including three elements: place, transition and arc. Among them, the place represents the state of the system; the transition represents the event or behavior and state changes that occur in the system, and the occurrence of the change is controlled by the place; the arc represents the relationship between the local state and the change. Another important component in the Petri net model is token, which is included in the warehouse. As the task progresses, when a certain change is stimulated, some preconditions will no longer hold, and another posterior condition will be met at the same time. At this time, tokens can flow to different places in the direction of the arc, thereby dynamically describing Changes in system status. The characteristic of token is in which place it exists, it is true, otherwise it is false.
[0055] The Petri net hexagram is...
PUM
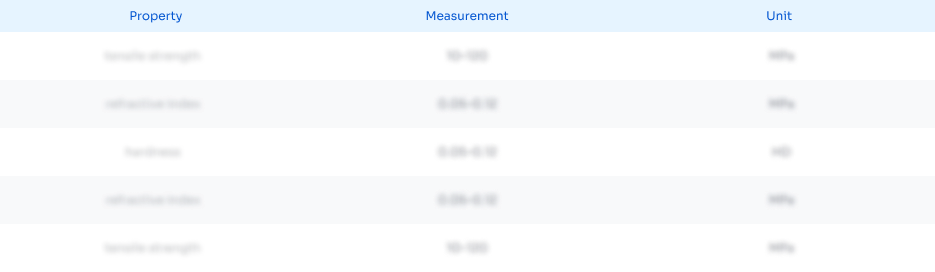
Abstract
Description
Claims
Application Information

- R&D Engineer
- R&D Manager
- IP Professional
- Industry Leading Data Capabilities
- Powerful AI technology
- Patent DNA Extraction
Browse by: Latest US Patents, China's latest patents, Technical Efficacy Thesaurus, Application Domain, Technology Topic, Popular Technical Reports.
© 2024 PatSnap. All rights reserved.Legal|Privacy policy|Modern Slavery Act Transparency Statement|Sitemap|About US| Contact US: help@patsnap.com