Dehydration process used in alkyd or polyester resin synthesis
A technology of polyester resin and alkyd resin, which is applied in the dehydration process field in the synthesis of alkyd or polyester resin, and can solve the problems of benzene series residue, large material loss, xylene residue, etc.
- Summary
- Abstract
- Description
- Claims
- Application Information
AI Technical Summary
Problems solved by technology
Method used
Examples
Embodiment 1
[0028] Step 1. Add the dehydrating agent and the raw materials for synthesizing alkyd or polyester resin into the reaction kettle together. During the esterification reaction, the monomers of the esterification reaction are mixed with the dehydrating agent to obtain the esterification product and the dehydrating agent-water azeotrope Object; Wherein, the quality of described dehydrating agent is 3% of described monomer mass, and described dehydrating agent comprises methyl isobutyl ketone;
[0029] Step 2. After the synthesis of the alkyd resin or polyester resin is completed, separate the alkyd resin or polyester resin from the dehydrating agent-water azeotrope, at a temperature of 130° C., a pressure of 0.2 atm, and a reaction time of 2 hours. Obtain acid resin or polyester resin and dehydrating agent-water azeotrope; among them, dehydrating agent is slightly soluble in water, after standing, part of dehydrating agent and water layer, separate to obtain part of dehydrating ag...
Embodiment 2
[0034] Step 1. Add the dehydrating agent and synthetic alkyd or polyester resin raw materials into the reaction kettle together. When carrying out the esterification reaction, mix the monomers of the esterification reaction with the dehydrating agent to obtain the esterification product and the dehydrating agent-water azeotrope Object; Wherein, the quality of described dehydrating agent is 6% of described monomer mass, and described dehydrating agent comprises methyl isobutyl ketone;
[0035]Step 2. After the synthesis of the alkyd resin or polyester resin is completed, separate the alkyd resin or polyester resin from the dehydrating agent-water azeotrope, at a temperature of 150° C., a pressure of 0.3 atm, and a reaction time of 3 hours. Obtain acid resin or polyester resin and dehydrating agent-water azeotrope; among them, dehydrating agent is slightly soluble in water, after standing, part of dehydrating agent and water layer, separate to obtain part of dehydrating agent and...
Embodiment 3
[0040] Step 1. Add the dehydrating agent and the raw materials for synthesizing alkyd or polyester resin into the reaction kettle together. During the esterification reaction, the monomers of the esterification reaction are mixed with the dehydrating agent to obtain the esterification product and the dehydrating agent-water azeotrope Object; Wherein, the quality of described dehydrating agent is 5% of described monomer mass, and described dehydrating agent comprises methyl isobutyl ketone;
[0041] Step 2. After the synthesis of the alkyd resin or polyester resin is completed, separate the alkyd resin or polyester resin from the dehydrating agent-water azeotrope, at a temperature of 140° C., a pressure of 0.2 atm, and a reaction time of 2.5 hours. Obtain acid resin or polyester resin and dehydrating agent-water azeotrope; among them, dehydrating agent is slightly soluble in water, after standing, part of dehydrating agent and water layer, separate to obtain part of dehydrating ...
PUM
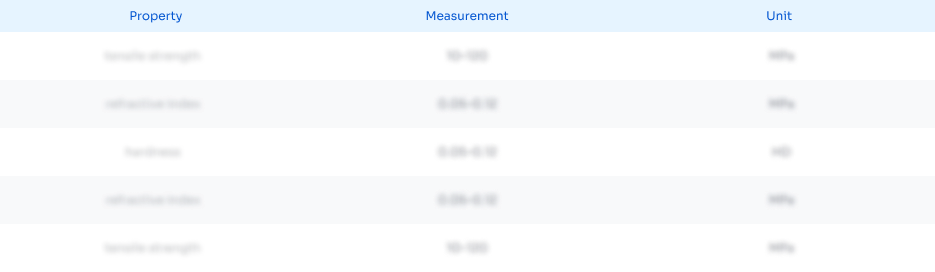
Abstract
Description
Claims
Application Information

- R&D Engineer
- R&D Manager
- IP Professional
- Industry Leading Data Capabilities
- Powerful AI technology
- Patent DNA Extraction
Browse by: Latest US Patents, China's latest patents, Technical Efficacy Thesaurus, Application Domain, Technology Topic, Popular Technical Reports.
© 2024 PatSnap. All rights reserved.Legal|Privacy policy|Modern Slavery Act Transparency Statement|Sitemap|About US| Contact US: help@patsnap.com