Automatic calibration system and method of permanent magnet synchronous motor for electric vehicles
A technology of permanent magnet synchronous motor and automatic calibration system, which is applied in the direction of motor generator test, measurement of electricity, measurement of electric variables, etc., can solve the problems of long calibration period, unsatisfactory accuracy, and long time consumption.
- Summary
- Abstract
- Description
- Claims
- Application Information
AI Technical Summary
Problems solved by technology
Method used
Image
Examples
Embodiment Construction
[0029] Example figure 1As shown, the automatic calibration system of the permanent magnet synchronous motor for electric vehicles of the present invention includes a DC power supply 1, a motor under test 2 and a dynamometer 3, the motor under test 2 is connected to the dynamometer with 3 shafts, and the system also includes a first A motor controller 4, a second motor controller 5, a torque speed sensor 6, an information sending unit 7 and an industrial computer 8, the DC power supply 1 is electrically connected to the first motor controller 4 and the second motor controller 5 respectively connected to provide a DC voltage, the first motor controller 4 and the second motor controller 5 are electrically connected to the motor under test 2 and the dynamometer 3 respectively and control the motor under test 2 and the dynamometer 3 to run, so The torque speed sensor 6 is mechanically connected with the motor under test 2 and the dynamometer 3 to collect torque and speed informatio...
PUM
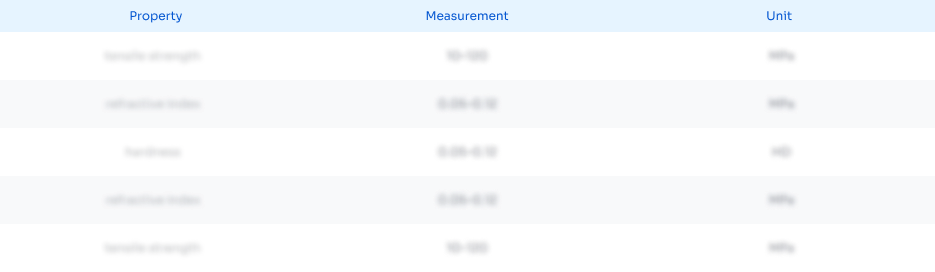
Abstract
Description
Claims
Application Information

- Generate Ideas
- Intellectual Property
- Life Sciences
- Materials
- Tech Scout
- Unparalleled Data Quality
- Higher Quality Content
- 60% Fewer Hallucinations
Browse by: Latest US Patents, China's latest patents, Technical Efficacy Thesaurus, Application Domain, Technology Topic, Popular Technical Reports.
© 2025 PatSnap. All rights reserved.Legal|Privacy policy|Modern Slavery Act Transparency Statement|Sitemap|About US| Contact US: help@patsnap.com