Direct driving device of self-bearing motor
A driving device and bearing motor technology, applied in the direction of electromechanical devices, electric components, electrical components, etc., can solve the problems of large mechanical friction torque, complex control system, difficult transportation, etc., to eliminate friction torque, high transmission efficiency, maintenance low cost effect
- Summary
- Abstract
- Description
- Claims
- Application Information
AI Technical Summary
Problems solved by technology
Method used
Image
Examples
Embodiment 1
[0048] Embodiment 1, self-bearing motor direct drive device, such as figure 1 , figure 2 As shown, the self-bearing direct drive device of the present invention is mainly composed of a base 1, a direct drive motor 4, a radial active magnetic suspension bearing 5, a radial active magnetic suspension bearing position sensor 9, a rotary table 10, an axial protection bearing 36, Axial active offset magnetic suspension bearing unit upper 35, axial active offset magnetic suspension bearing unit lower 37, axial active offset magnetic suspension bearing position sensor 8, axial active offset magnetic suspension bearing unit 40, flexible connection parts 17. Mandrel adapter plate 13, mandrel 19, radial protection bearing 21, bearing seat 26, angular displacement sensor 27, reading head 30, sealing end cover 31, and mandrel protection end cover 12. The self-bearing direct drive device is placed horizontally, and the load is installed on the rotary table 10. Initialization is carried ...
PUM
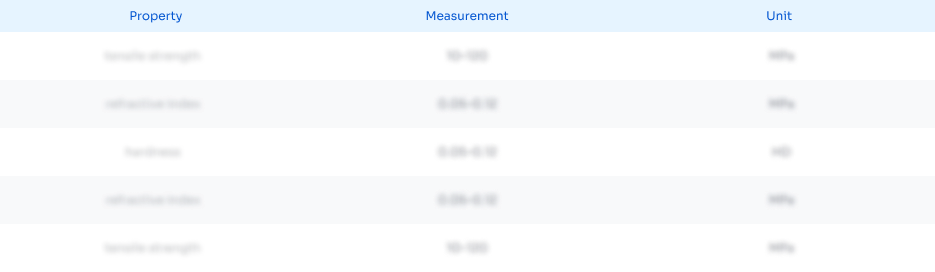
Abstract
Description
Claims
Application Information

- R&D Engineer
- R&D Manager
- IP Professional
- Industry Leading Data Capabilities
- Powerful AI technology
- Patent DNA Extraction
Browse by: Latest US Patents, China's latest patents, Technical Efficacy Thesaurus, Application Domain, Technology Topic, Popular Technical Reports.
© 2024 PatSnap. All rights reserved.Legal|Privacy policy|Modern Slavery Act Transparency Statement|Sitemap|About US| Contact US: help@patsnap.com