Device and method for simultaneous detection of displacement and sucking capillary force curves under oil reservoir conditions
A technology of capillary force and conditions, applied in measuring devices, suspension and porous material analysis, instruments, etc., can solve the problems that the centrifugation method is difficult to simulate the characteristics of reservoir conditions, cannot be mixed, and the displacement and sucking process are very different.
- Summary
- Abstract
- Description
- Claims
- Application Information
AI Technical Summary
Problems solved by technology
Method used
Image
Examples
Embodiment 1
[0045] Such as figure 1 As shown, the device for joint measurement of displacement and suction capillary force curves under reservoir conditions includes: triaxial stress core holder 5, which is a cylindrical core holder placed horizontally, three The axial stress core holder has a pressure resistance of 60MPa; the triaxial stress core holder 5 is equipped with a rubber tube and plugs at both ends; the rubber tube is equipped with a core 6, and one end of the core 6 is equipped with a non-wetting phase semi-permeable partition 7 , the other end is provided with a wetting phase semi-permeable partition 8; a non-wetting phase semi-permeable partition 7 and a wetting phase semi-permeable partition 8 are respectively in contact with the plugs at both ends of the triaxial stress core holder 5, and the non-wetting phase The phase semi-permeable partition 7 can allow the non-wetting phase fluid to pass through while preventing the wetting phase fluid from passing through, and the wet...
Embodiment 2
[0082] Such as figure 2 As shown, the displacement and suction capillary force curve joint measurement device group under reservoir conditions includes three sets of triaxial stress core holders, three sets of non-wetting phase back pressure controllers, and three sets of non-wetting phase pressure flow sensors Three sets of non-wetting phase fluid metering tubes, three sets of wetting phase back pressure controllers, three sets of wetting phase pressure flow sensor groups, three sets of wetting phase fluid metering tubes, three sets of non-wetting phase semi-permeable barriers plate, three sets of semi-permeable partitions for wetting phase, one set of constant speed and constant pressure micropump, one set of piston container for non-wetting phase fluid, one set of piston container for wetting phase fluid, pressure gauge, and one set of ring-pressing axial pressure mechanical pump , a set of back pressure mechanical pumps, and a computer; among them: the ring pressure axial...
PUM
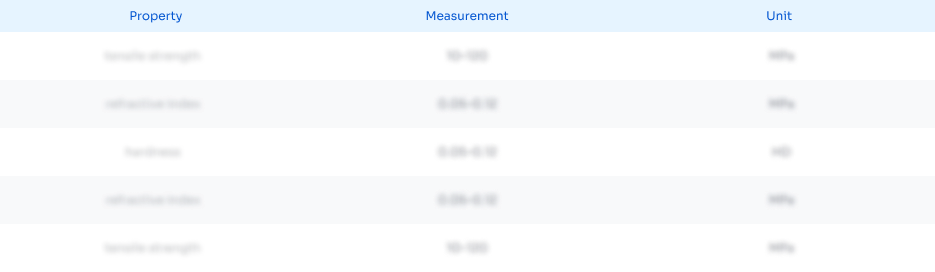
Abstract
Description
Claims
Application Information

- Generate Ideas
- Intellectual Property
- Life Sciences
- Materials
- Tech Scout
- Unparalleled Data Quality
- Higher Quality Content
- 60% Fewer Hallucinations
Browse by: Latest US Patents, China's latest patents, Technical Efficacy Thesaurus, Application Domain, Technology Topic, Popular Technical Reports.
© 2025 PatSnap. All rights reserved.Legal|Privacy policy|Modern Slavery Act Transparency Statement|Sitemap|About US| Contact US: help@patsnap.com