Board tensile deformation based robot bending precision compensating method
A technology of tensile deformation and precision compensation, applied in the direction of instruments, simulators, computer control, etc., can solve the problem of low bending accuracy of robots, and achieve the effect of eliminating pulling or squeezing and improving bending accuracy.
- Summary
- Abstract
- Description
- Claims
- Application Information
AI Technical Summary
Problems solved by technology
Method used
Image
Examples
Embodiment Construction
[0045] The present invention will be described in detail below in conjunction with the embodiments and accompanying drawings.
[0046] The implementation steps are as follows:
[0047] Step 1: Use the robot to calibrate the three points on the notch, and the coordinate value of the origin O is P O (1896.72, -239.85, 1033.50), calibrate the point P in the X-axis direction of the compensation coordinate system along the slot direction A (1835.10, -1672.77, 1038.03), point P in the XY plane direction of the calibration compensation coordinate system B (1856.89, -1437.79, 1037.22), calculate the X, Y, Z axis unit vectors of the compensation coordinate system respectively, and obtain the rotation matrix as follows:
[0048]
[0049] According to the Z-Y-Z Euler transformation formula, the rotation matrix R S Calculate A=-92.46, B=0, C=0, and thus obtain the compensation coordinate system as follows:
[0050] S=(1896.72, -239.85, 1033.50, -92.46, 0, 0)
[0051] Step 2: Obtai...
PUM
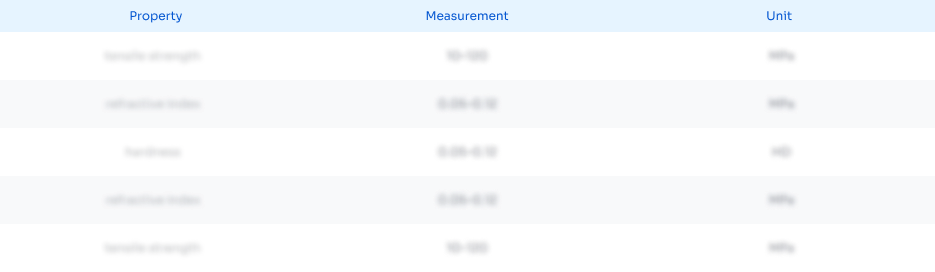
Abstract
Description
Claims
Application Information

- R&D
- Intellectual Property
- Life Sciences
- Materials
- Tech Scout
- Unparalleled Data Quality
- Higher Quality Content
- 60% Fewer Hallucinations
Browse by: Latest US Patents, China's latest patents, Technical Efficacy Thesaurus, Application Domain, Technology Topic, Popular Technical Reports.
© 2025 PatSnap. All rights reserved.Legal|Privacy policy|Modern Slavery Act Transparency Statement|Sitemap|About US| Contact US: help@patsnap.com