Preparation method of wet-mixed mortar with high water retention rate
A technology of wet-mixing mortar and water retention rate, which is applied in the field of wet-mixing mortar, which can solve the problems of low civilized construction, unstable mortar quality, and single mortar variety, so as to prolong the operation time of construction, ensure the continuity of use, and disperse mortar The effect of cementitious materials
- Summary
- Abstract
- Description
- Claims
- Application Information
AI Technical Summary
Problems solved by technology
Method used
Examples
Embodiment 1
[0014] A method for preparing wet-mixed mortar with a high water retention rate, comprising the following steps: stirring 40kg of cinder, 120kg of tailings machine-made sand, 40kg of cement, 14kg of diatomaceous earth, 10kg of castor oil compound, and 80kg of water for 50 minutes, and adding 8kg of plastic stabilizer , 6kg of glass fiber, 8kg of retarder, and 4kg of water reducer are stirred evenly to obtain a wet-mixed mortar with a high water retention rate.
[0015] The castor oil compound is prepared by the following process: mix 40kg castor oil, 0.1kg dibutyltin dilaurate, and 4kg toluene diisocyanate, heat up to 85°C and stir for 50min under nitrogen protection, add 20kg epoxy soybean oil and continue stirring for 20min, add 2kg Phthalic anhydride and 0.5kg N,N-dimethylbenzylamine were heated up to 125°C and stirred for 25 minutes to obtain a castor oil complex.
Embodiment 2
[0017] A method for preparing wet-mixed mortar with a high water retention rate, comprising the following steps: stirring 60kg of coal slag, 100kg of tailings machine-made sand, 60kg of cement, 10kg of diatomaceous earth, 16kg of castor oil compound, and 60kg of water for 70 minutes, and adding 4kg of plastic stabilizer , 12kg of glass fiber, 4kg of retarder, and 8kg of water reducer are stirred evenly to obtain a wet-mixed mortar with a high water retention rate.
[0018] The castor oil complex is prepared by the following process: mix 30kg castor oil, 0.2kg dibutyltin dilaurate, and 2kg toluene diisocyanate, heat up to 95°C and stir for 30min under nitrogen protection, add 30kg epoxy soybean oil and continue stirring for 10min, add 4kg Phthalic anhydride and 0.3kg N,N-dimethylbenzylamine were heated up to 135°C and stirred for 15 minutes to obtain a castor oil complex.
Embodiment 3
[0020] A method for preparing wet-mixed mortar with a high water retention rate, comprising the following steps: stirring 45kg of coal slag, 115kg of tailings machine-made sand, 45kg of cement, 13kg of diatomaceous earth, 12kg of castor oil compound, and 75kg of water for 55 minutes, and adding 7kg of plastic stabilizer , 8kg glass fiber, 7kg retarder, and 5kg water reducer are stirred evenly to obtain a wet-mixed mortar with a high water retention rate.
[0021] The castor oil complex is prepared by the following process: mix 37kg castor oil, 0.12kg dibutyltin dilaurate, and 3.5kg toluene diisocyanate, heat up to 88°C and stir for 45min under nitrogen protection, add 22kg epoxy soybean oil and continue stirring for 18min, add 2.5kg of phthalic anhydride and 0.45kg of N,N-dimethylbenzylamine were heated up to 128°C and stirred for 22 minutes to obtain a castor oil complex.
PUM
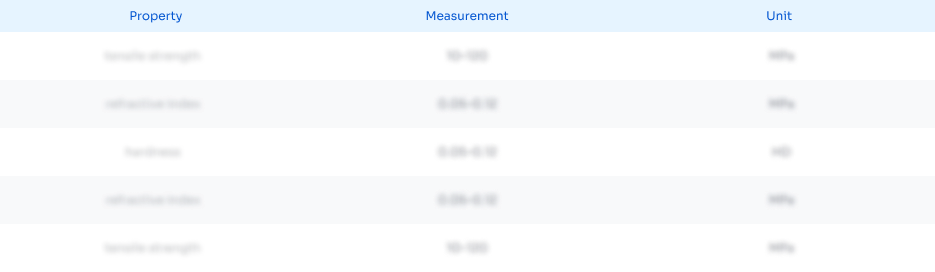
Abstract
Description
Claims
Application Information

- Generate Ideas
- Intellectual Property
- Life Sciences
- Materials
- Tech Scout
- Unparalleled Data Quality
- Higher Quality Content
- 60% Fewer Hallucinations
Browse by: Latest US Patents, China's latest patents, Technical Efficacy Thesaurus, Application Domain, Technology Topic, Popular Technical Reports.
© 2025 PatSnap. All rights reserved.Legal|Privacy policy|Modern Slavery Act Transparency Statement|Sitemap|About US| Contact US: help@patsnap.com