A Fatigue Fracture Blanking Machine for Circumferential Cyclic Loading of Workpieces with Unmoved Fatigue Loads
A technology of fatigue loading and cyclic loading, applied in manufacturing tools, metal processing equipment, storage devices, etc., can solve the problems of poor section quality, low production efficiency, high energy consumption, etc., and achieve good section quality, simple structure, and high efficiency. Effect
- Summary
- Abstract
- Description
- Claims
- Application Information
AI Technical Summary
Problems solved by technology
Method used
Image
Examples
Embodiment Construction
[0022] The present invention will be described in detail below in conjunction with the accompanying drawings and specific embodiments.
[0023] see figure 1 The present invention provides a fatigue fracture blanking machine that does not move the workpiece fatigue load and is loaded circularly in the circumferential direction. It consists of three parts: a loading frequency control mechanism, a fatigue load loading mechanism and a workpiece clamping mechanism.
[0024] see figure 2 , the loading frequency control mechanism includes a box body 2 and a frequency conversion speed regulation three-phase asynchronous motor 1 arranged on the box body 2 and a main shaft 5 arranged in the box body 2, and the two ends of the main shaft 5 pass through the box body 2 and are exposed. Frequency conversion and speed regulation three-phase asynchronous motor 1 has a large pulley 3, the end of the main shaft 5 on the same side as the large pulley 3 has a small pulley 6, the large pulley 3 ...
PUM
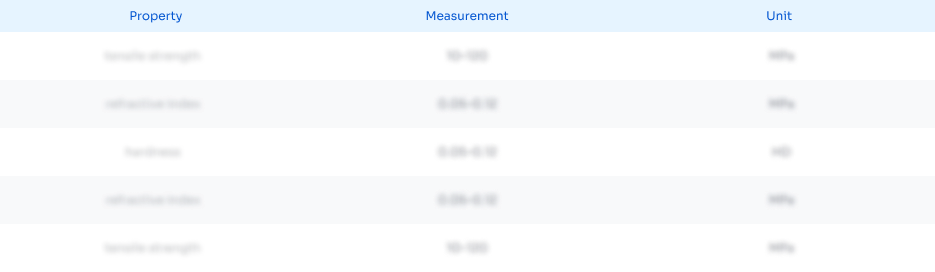
Abstract
Description
Claims
Application Information

- R&D
- Intellectual Property
- Life Sciences
- Materials
- Tech Scout
- Unparalleled Data Quality
- Higher Quality Content
- 60% Fewer Hallucinations
Browse by: Latest US Patents, China's latest patents, Technical Efficacy Thesaurus, Application Domain, Technology Topic, Popular Technical Reports.
© 2025 PatSnap. All rights reserved.Legal|Privacy policy|Modern Slavery Act Transparency Statement|Sitemap|About US| Contact US: help@patsnap.com