Ball-joint-based pneumatic manipulator
A technology of ball joints and operating arms, which is applied in medical science, surgery, surgical instrument support, etc., can solve the problem that the attending doctor cannot operate multiple surgical instruments at the same time, so as to improve the stability of surgery, reduce the probability of error, and reduce labor. intensity effect
- Summary
- Abstract
- Description
- Claims
- Application Information
AI Technical Summary
Problems solved by technology
Method used
Image
Examples
Embodiment 1
[0030] Such as Figures 1 to 3 As shown, a pneumatically operated arm based on a ball joint includes a connecting rod 1 and a joint connecting rod 1-5, wherein the joint connecting rod 1-5 is connected to the ball joint mechanism module 1-1 of the connecting rod 1 , the connecting rod 1 includes a ball joint mechanism module 1-1, a connecting cylinder 1-2, a cover plate 1-3, a three-way joint 1-4, and an air pipe 1-6, and the two ends of the connecting cylinder 1-2 A ball joint mechanism module 1-1 is installed respectively, and the three-way joint 1-4 is installed inside the connecting cylinder 1-2. The other end of 1-4 passes through the cover plate 1-3, and the cover plate 1-3 is installed on the connecting cylinder 1-2, and the cover plate 1-3 locks the tee joint 1-4 in the connecting cylinder 1-2; pneumatic operation The connecting rod 1 of the arm is connected by two ball joint mechanism modules 1-1 at both ends of the hollow connecting cylinder 1-2, and the two ends of...
Embodiment 2
[0038] Such as Figure 4 As shown, this embodiment is obtained by transforming the head end form of the ejector rod 2-7 in the first embodiment on the basis of the first embodiment, for example, transforming the coaxial conical surface in the first embodiment into a The -7 axis is formed by a curved surface with a certain eccentricity Figure 4 The eccentric push rod 2-13 of (a). Or retain the outer surface of the ejector rod 2-7, and remove the material of the ejector rod 2-7 from the outside to the inside to form Figure 4 Concave ejector pin 2-14 shape in (b). Other unmentioned components are the same as those in Embodiment 1 without change.
Embodiment 3
[0040] Such as Figure 5 As shown, this embodiment is obtained on the basis of Embodiment 1. What is changed in this embodiment is that the numbers of guide rods and springs are arranged uniformly or non-uniformly, while other parts and structures are the same as Embodiment 1. Illustrate as: by changing the kind or the quantity of guide rod 2-7, eccentric push rod 2-13, concave push rod 2-14 installed on the front piston 2-6. E.g Figure 5 (a) three guide rods 2-7 and corresponding springs 2-9 are installed; Figure 5 Four guide rods 2-7 and corresponding springs are installed in (b). Figure 5 (a) shows a uniform arrangement by changing the number of guide rods and springs; Figure 5 (b) shows that the number of guide rods and springs is changed for non-uniform arrangement.
PUM
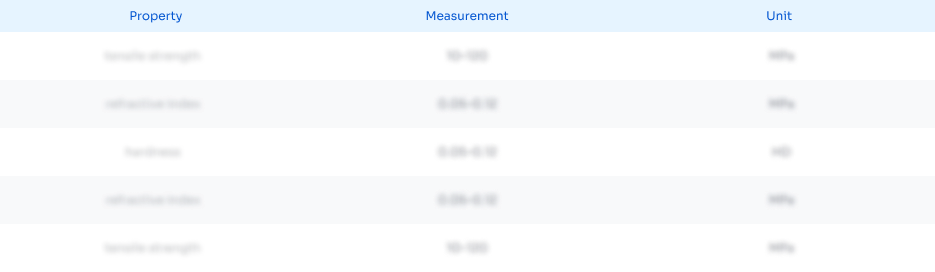
Abstract
Description
Claims
Application Information

- R&D
- Intellectual Property
- Life Sciences
- Materials
- Tech Scout
- Unparalleled Data Quality
- Higher Quality Content
- 60% Fewer Hallucinations
Browse by: Latest US Patents, China's latest patents, Technical Efficacy Thesaurus, Application Domain, Technology Topic, Popular Technical Reports.
© 2025 PatSnap. All rights reserved.Legal|Privacy policy|Modern Slavery Act Transparency Statement|Sitemap|About US| Contact US: help@patsnap.com