Film tearing method for sequentially tearing top films and bottom films of OLED (organic light-emitting diode) materials
A top film and bottom film technology, which is applied in the field of OLED materials, can solve the problems of OLED material bending, wear and tear film success rate, etc., and achieve the effect of high film tearing efficiency and avoid bending
- Summary
- Abstract
- Description
- Claims
- Application Information
AI Technical Summary
Problems solved by technology
Method used
Image
Examples
Embodiment 1
[0044] This embodiment provides a film tearing device that successively tears the OLED material top film and bottom film, such as figure 1 with figure 2 As shown, it includes a feeding device 1, a front tearing device 2, a rear tearing device 3, a dust removal device 5, a receiving device 4, and the OLED material is placed on the feeding device 1, the front tearing device 2, and the rear tearing device 3 , the dust removal device 5, the horizontal transmission device (specifically a belt conveyor) for transmission between the dust removal device 5 and the receiving device 4; the feeding device 1 is used to place the OLED material without tearing the film on the horizontal transmission device, including for placing A discharge tray 11 for OLED materials, a lifting drive mechanism 12 for driving the discharge tray 11 up and down, a rotary conveying assembly 13 for the feeding section, and a workbench 14 for the feeding device;
[0045] Preferably, the discharge tray 11 is squa...
Embodiment 2
[0070] This embodiment provides a film tearing method for successively tearing off the top film and the bottom film of the OLED material, and the film tearing method will be described in detail in conjunction with the film tearing device for successively tearing the top film and the bottom film of the OLED material in Example 1.
[0071] A film tearing method for successively tearing the top film and the bottom film of the OLED material, the specific steps are:
[0072] First, place the OLED materials with protective films on both sides on the horizontal conveying device one by one through the feeding device 1, the specific steps are as follows:
[0073] A number of OLED materials with protective films on both sides are laminated and placed on the discharge tray 11;
[0074] Through the lifting drive mechanism 12, the discharge tray 11 is moved upward so that the rotary conveying assembly 13 of the feeding section can take the OLED material;
[0075] The OLED material on the ...
PUM
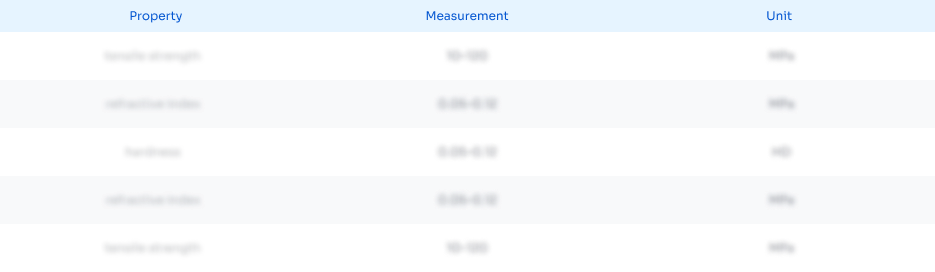
Abstract
Description
Claims
Application Information

- R&D Engineer
- R&D Manager
- IP Professional
- Industry Leading Data Capabilities
- Powerful AI technology
- Patent DNA Extraction
Browse by: Latest US Patents, China's latest patents, Technical Efficacy Thesaurus, Application Domain, Technology Topic, Popular Technical Reports.
© 2024 PatSnap. All rights reserved.Legal|Privacy policy|Modern Slavery Act Transparency Statement|Sitemap|About US| Contact US: help@patsnap.com