Automatic double-shaft position correction device
An automatic, motor-driven circuit technology, applied in the direction of using feedback control, closed-circuit television system, etc., can solve the problems of image shaking, inability to effectively monitor the position, and the inability of the pan/tilt to return, and achieve the effect of improving absolute accuracy
- Summary
- Abstract
- Description
- Claims
- Application Information
AI Technical Summary
Problems solved by technology
Method used
Image
Examples
Embodiment 1
[0008] Embodiment 1: refer to figure 1 . A dual-axis position automatic correction device, including PC terminal, camera, gyroscope, PTZ control MCU, motor drive circuit, horizontal control motor, vertical control motor, power conversion circuit, power interface, network interface, camera, gyroscope They are respectively electrically connected to the pan-tilt control MCU, and the pan-tilt control MCU is electrically connected to the motor drive circuit. The control terminals of the horizontal control motor and the vertical control motor are respectively controlled and connected by the motor drive circuit, and the power conversion circuit will be input through the power interface. The power supply is converted into DC power supply to the camera, gyroscope, pan-tilt control MCU and motor drive circuit, and the camera communicates with the PC through the network interface. The dual-axis position automatic correction device also includes a camera installation compartment 1 for in...
PUM
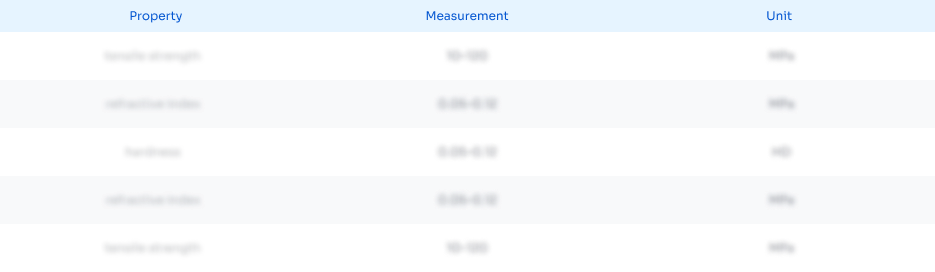
Abstract
Description
Claims
Application Information

- R&D Engineer
- R&D Manager
- IP Professional
- Industry Leading Data Capabilities
- Powerful AI technology
- Patent DNA Extraction
Browse by: Latest US Patents, China's latest patents, Technical Efficacy Thesaurus, Application Domain, Technology Topic, Popular Technical Reports.
© 2024 PatSnap. All rights reserved.Legal|Privacy policy|Modern Slavery Act Transparency Statement|Sitemap|About US| Contact US: help@patsnap.com