High-temperature inductance paint-removing tin-soldering integrated machine
A technology of stripping and welding, all-in-one machine, applied in inductor/transformer/magnet manufacturing, circuits, electrical components, etc., can solve the problems of high temperature liquid tin fading, inductance production line unable to complete high temperature inductance batch automatic production, low efficiency, etc. The effect of improving production efficiency
- Summary
- Abstract
- Description
- Claims
- Application Information
AI Technical Summary
Problems solved by technology
Method used
Image
Examples
Embodiment Construction
[0022] Such as Figure 1-4 As shown, the high-temperature inductance paint stripping and soldering all-in-one machine of the present invention includes a frame 1, a vibration plate 2 is arranged in front of the frame 1, a wave soldering machine 3 is arranged at the rear of the frame 1, and a driving motor is arranged on the frame 1 and two sets of transmission mechanisms, the two sets of transmission mechanisms are arranged side by side;
[0023] Every group of transmission mechanism comprises two turning wheels 4 and several supporting wheels 5, and the center line of turning wheels 4 and supporting wheels 5 is all vertically arranged, and wherein a turning wheel 4 is connected to the front end of frame 1 in rotation, and another turning wheel 4 Rotationally connected to the rear end of the frame 1, a conveyor belt 6 is connected between the two rotating wheels 4, the length direction of the conveyor belt 6 is consistent with the length direction of the frame 1, and several s...
PUM
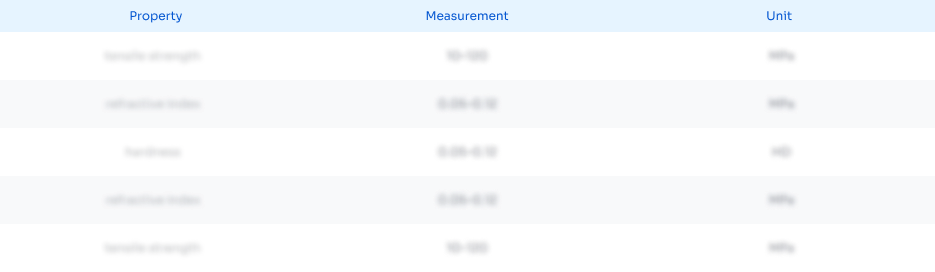
Abstract
Description
Claims
Application Information

- R&D
- Intellectual Property
- Life Sciences
- Materials
- Tech Scout
- Unparalleled Data Quality
- Higher Quality Content
- 60% Fewer Hallucinations
Browse by: Latest US Patents, China's latest patents, Technical Efficacy Thesaurus, Application Domain, Technology Topic, Popular Technical Reports.
© 2025 PatSnap. All rights reserved.Legal|Privacy policy|Modern Slavery Act Transparency Statement|Sitemap|About US| Contact US: help@patsnap.com