Fabricated building
A prefabricated and architectural technology, applied in buildings, building components, building structures, etc., can solve the problems of unguaranteed construction quality, serious environmental pollution, and high construction costs, and achieve convenient and fast installation, uniform quality, and simplified construction procedures. Effect
- Summary
- Abstract
- Description
- Claims
- Application Information
AI Technical Summary
Problems solved by technology
Method used
Image
Examples
Embodiment 1
[0039] Such as Figure 6 As shown, the present invention provides a prefabricated building, comprising a steel structure frame 4 and prefabricated exterior wall panels, specifically as Figure 6 As shown, the steel structure frame 4 is a rectangular frame, and the exterior wall panels include four walls connected end to end in sequence, each side wall is provided with a first wall panel 1, and the four first wall panels The boards 1 are respectively connected to the outside of the steel structure frame 4 through connectors 3, and the bottom end of the channel steel frame on each of the first wall boards 1 is connected to the adjacent first wall board 1. The welding parts 19 on the top are welded; in this way, the first wall panel 1 is prefabricated in the factory, so that there is no need to pour concrete on site to manufacture the cavity, which can solve the problem of large transportation volume, high construction cost and high construction cost of the method of pouring conc...
Embodiment 2
[0047] This embodiment is substantially the same as the technical solution in Embodiment 1, the main difference is that the exterior wall panel in this embodiment includes both the first wall panel 1 and the second wall panel 2, and the exterior wall panel also includes the first wall panel Two wallboards 2, the second wallboard 2 includes a frame-shaped second channel steel frame 28 and a second wall, and the second channel steel frame 28 is sleeved on the outside of the second wall; The two walls include the third fiberglass mesh layer 22, the third steel wire mesh layer 22, the third cement foam layer 23, the second thermal insulation layer 24, the fourth cement foam layer 25, the fourth fiberglass mesh layer 22 connected from top to bottom. Steel mesh layer 26 and fourth fiberglass mesh layer 27 .
[0048] The steel structure frame 4 is a rectangular frame, and the exterior wall panel includes a first wall, a second wall, a third wall and a fourth wall connected end to end...
PUM
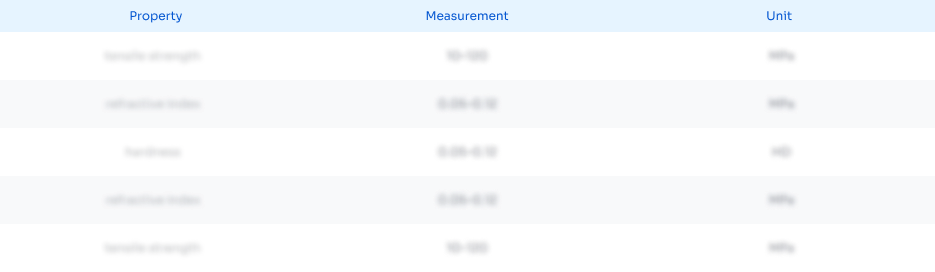
Abstract
Description
Claims
Application Information

- R&D Engineer
- R&D Manager
- IP Professional
- Industry Leading Data Capabilities
- Powerful AI technology
- Patent DNA Extraction
Browse by: Latest US Patents, China's latest patents, Technical Efficacy Thesaurus, Application Domain, Technology Topic, Popular Technical Reports.
© 2024 PatSnap. All rights reserved.Legal|Privacy policy|Modern Slavery Act Transparency Statement|Sitemap|About US| Contact US: help@patsnap.com