A method of stereo vision measurement of objects in vibration and small-sized space
A stereoscopic vision measurement and space-based technology, applied in the field of visual measurement, can solve problems such as difficult small-sized space layout, camera vibration interference, etc., to achieve the effects of ensuring measurement accuracy, improving matching accuracy, and reducing costs
- Summary
- Abstract
- Description
- Claims
- Application Information
AI Technical Summary
Problems solved by technology
Method used
Image
Examples
Embodiment 1
[0031] For a certain application scenario, the size of the measurement area is 500*500mm, the distance from the measurement object to the optical observation window is D1=1000mm, and the size of the optical observation window is 200*200mm. Such as image 3 As shown, the parameters of the optical imaging system are: the resolution of the camera is 2 million pixel black and white camera, the width of the image sensor is w=6.4mm, the distance between the lens and the prism is D2=100mm, the prism is made of optical glass, the refractive index is 1.6, and the width of the prism is Wb =100mm, height Hb=100mm, thickness Bb=26.5mm, prism angle.
Embodiment 2
[0033] The black and white checkerboard calibration board is used for the calibration of the measurement system. The specific method is: within the shooting field of view, the calibration board is placed multiple times in different postures, and the camera collects multiple frames of images. Such as figure 2 As shown, the captured image is divided into left and right view images IL and IR along the central axis, and then Zhang Zhengyou's binocular vision calibration method is used to calibrate the binocular vision measurement system and correct the lens distortion.
[0034] During actual measurement, the visual measurement system captures the image I of the measured object, divides the image at the central axis position, and obtains the left and right view images IL and IR, and uses them for binocular vision measurement according to the calibration results of the binocular vision measurement system.
Embodiment 3
[0036] The double prism and the camera are fixed by a mechanical fixing device to prevent relative displacement during the vibration process; 10 circular artificial marker points are set as reference points within the field of view of the camera, and the camera can capture the reference points during the vibration process.
[0037] The vibration correction method is:
[0038] 1) Before vibration, take the image of the reference point and calculate the initial coordinate X0 of the reference point;
[0039] 2) During the vibration process, take the image of the reference point, calculate the coordinate Xi of the reference point, and then calculate the conversion matrix P from the current coordinate to the initial coordinate: make X0=Xi*P, and the calculation method adopts the least square estimation;
[0040] 3) Transformation matrix P, coordinate transformation of the current three-dimensional measurement result Y of the surface of the measured object: Y’=Y*P, to eliminate vibrat...
PUM
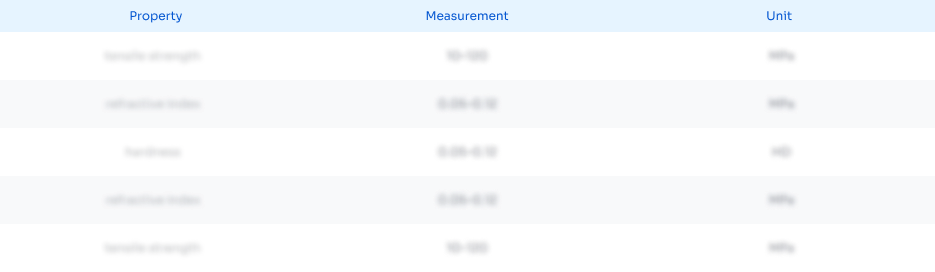
Abstract
Description
Claims
Application Information

- R&D Engineer
- R&D Manager
- IP Professional
- Industry Leading Data Capabilities
- Powerful AI technology
- Patent DNA Extraction
Browse by: Latest US Patents, China's latest patents, Technical Efficacy Thesaurus, Application Domain, Technology Topic, Popular Technical Reports.
© 2024 PatSnap. All rights reserved.Legal|Privacy policy|Modern Slavery Act Transparency Statement|Sitemap|About US| Contact US: help@patsnap.com