A Grinding Gap and Anti-Collision Method Based on Power Signal
A power signal and anti-collision technology, which is applied to the parts of grinding machine tools, grinding/polishing equipment, grinding automatic control devices, etc. In order to improve the efficiency of grinding process and the quality of grinding process
- Summary
- Abstract
- Description
- Claims
- Application Information
AI Technical Summary
Problems solved by technology
Method used
Image
Examples
Embodiment Construction
[0017] Such as figure 1 As shown in the diagram of the void elimination and anti-collision monitoring system, the power sensor is installed at the output end of the machine tool spindle inverter, and the data acquisition control card is connected to the signal line of the power sensor, and the following 1), 2), 3), 4 ), 5) and 6) steps are embedded in the data acquisition control card, and the switch input / output of the data acquisition control card is connected with the numerical control system of the CNC machine tool, and the machining cycle program of the CNC machine tool is started to complete the void elimination / anti-collision function.
[0018] Such as figure 2 The schematic diagram of the blanking distance monitoring power signal and the input / output signal of the control card shown is image 3 The flow chart of the realization of void elimination and anti-collision shown in the figure, the realization of the grinding void elimination and anti-collision method based ...
PUM
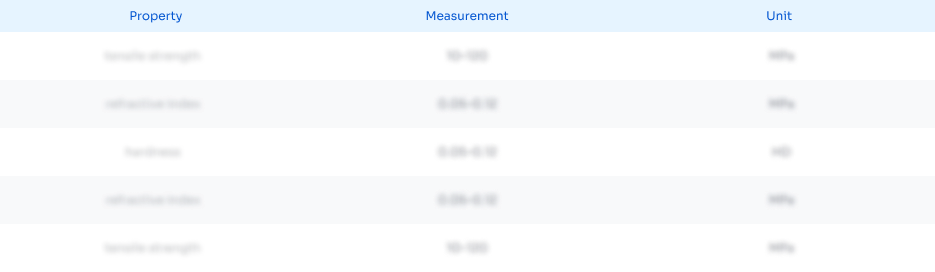
Abstract
Description
Claims
Application Information

- Generate Ideas
- Intellectual Property
- Life Sciences
- Materials
- Tech Scout
- Unparalleled Data Quality
- Higher Quality Content
- 60% Fewer Hallucinations
Browse by: Latest US Patents, China's latest patents, Technical Efficacy Thesaurus, Application Domain, Technology Topic, Popular Technical Reports.
© 2025 PatSnap. All rights reserved.Legal|Privacy policy|Modern Slavery Act Transparency Statement|Sitemap|About US| Contact US: help@patsnap.com