Composite sludge conditioner based on iron-containing sludge pyrolysis residue as well as preparation and application of composite sludge conditioner
A conditioner and sludge technology, applied in water/sludge/sewage treatment, sludge treatment, dehydration/drying/concentrated sludge treatment, etc., can solve the problem of neglecting synergy, ineffective utilization of iron elements, and waste of resources and other problems to achieve the effect of convenient dehydration treatment
- Summary
- Abstract
- Description
- Claims
- Application Information
AI Technical Summary
Problems solved by technology
Method used
Image
Examples
Embodiment 1
[0062] The preparation and application method of the sludge pyrolysis residue based on iron-containing sludge in this embodiment is carried out according to the following steps:
[0063] (1) Put 17kg of sludge into the sludge conditioning tank and add 128.2g of FeSO 4·7H 2 O to stir, the stirring speed is 150rpm, the stirring time is 5min, then add 104.9mL of 30% hydrogen peroxide for stirring, the stirring speed is 100rpm, the stirring time is 30min, so that the oxidation reagent and the sludge fully react, and finally add 166g red mud, and quickly stir for conditioning, the stirring speed is 150rpm, and the stirring time is 5min. Among them, the percentage content of iron in red mud is 26%, the mass percentage content of aluminum oxide is 18%, the mass percentage content of titanium oxide is 6%, and the content percentage content of silicon dioxide and other minerals is 50%. Finally, 17.4kg of conditioned sludge was obtained.
[0064] (2) Use a plate and frame filter pres...
Embodiment 2
[0070] The preparation and application method of the sludge pyrolysis residue based on iron-containing sludge in this embodiment is carried out according to the following steps:
[0071] (1) Add 17kg of sludge into the sludge conditioning tank, add 58.57g of FeCl 2 Stir, the stirring speed is 150rpm, the stirring time is 5min, then add 104.9mL hydrogen peroxide with a purity of 30% for stirring, the stirring speed is 100rpm, the stirring time is 30min, so that the oxidation reagent and the sludge fully react, and finally add 15g Quicklime, and fast stirring for conditioning, the stirring speed is 150rpm, the stirring time is 5min, and finally 17.3kg of conditioned sludge is obtained.
[0072] (2) Use a plate and frame filter press to dehydrate the conditioning sludge. First pump 17.3kg of conditioning sludge into a sludge feeding tank with a volume of 50L, and finally use an air compressor to pump the sludge in the feeding tank. The conditioned sludge is pressed into the diap...
Embodiment 3
[0077] The preparation and application method of the sludge pyrolysis residue based on iron-containing sludge in this embodiment is carried out according to the following steps:
[0078] (1) Add 15.4kg of sludge into the sludge conditioning tank, add 73.92g of FeCl 2 Stir, the stirring speed is 150rpm, the stirring time is 5min, then add 154.1mL of 30% hydrogen peroxide for stirring, the stirring speed is 100rpm, and the stirring time is 30min, so that the oxidation reagent and the sludge fully react, and finally 15.4kg of conditioned sludge.
[0079] (2) Use a plate and frame filter press to dehydrate the conditioning sludge. First pump 15.4kg of conditioning sludge into a sludge feeding tank with a volume of 50L, and finally use an air compressor to pump the sludge in the feeding tank. The conditioned sludge is pressed into the diaphragm plate frame for dehydration. The pressure of the air compressor is gradually increased from 0 to 0.8MPa every 1min, and kept for 25min. O...
PUM
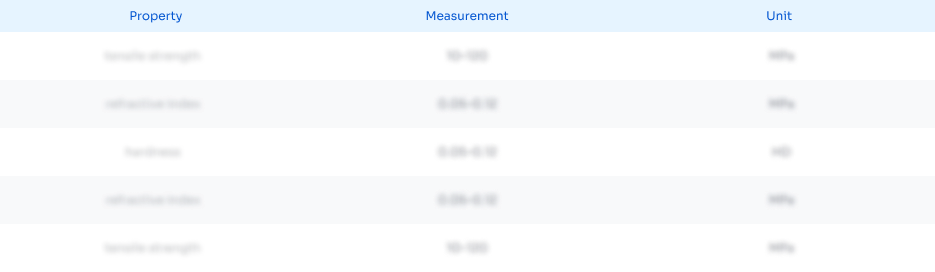
Abstract
Description
Claims
Application Information

- R&D
- Intellectual Property
- Life Sciences
- Materials
- Tech Scout
- Unparalleled Data Quality
- Higher Quality Content
- 60% Fewer Hallucinations
Browse by: Latest US Patents, China's latest patents, Technical Efficacy Thesaurus, Application Domain, Technology Topic, Popular Technical Reports.
© 2025 PatSnap. All rights reserved.Legal|Privacy policy|Modern Slavery Act Transparency Statement|Sitemap|About US| Contact US: help@patsnap.com