Torsional mode guided-wave magnetostrictive sensor based on double-ring permanent magnet array
A torsion mode, permanent magnet technology, applied in the direction of instruments, scientific instruments, material magnetic variables, etc., can solve the problems of current fluctuation, limited bias magnetic field strength, electromagnet current should not be too large, etc., to improve energy and static magnetic field The effect of uniform distribution and quick disassembly
- Summary
- Abstract
- Description
- Claims
- Application Information
AI Technical Summary
Benefits of technology
Problems solved by technology
Method used
Image
Examples
Embodiment Construction
[0021] According to the above content of the invention, the torsional mode guided wave magnetostrictive sensor based on the double-ring permanent magnet array can provide the following implementation modes.
[0022] The torsional mode guided wave magnetostrictive sensor based on the double-ring permanent magnet array can directly detect the defects of the pipeline quickly, and can also achieve long-term effective monitoring by using epoxy resin to glue the sensor in the pipe (or rod).
[0023] The following figures further illustrate the present invention in conjunction with the accompanying drawings and the above embodiments, and the specific implementation examples provided below are only descriptive, not restrictive, and cannot be used to limit the protection scope of the present invention.
[0024] like figure 1 It is a schematic diagram of the assembly of the torsional mode guided wave magnetostrictive sensor based on the double-ring permanent magnet array. The sensor is...
PUM
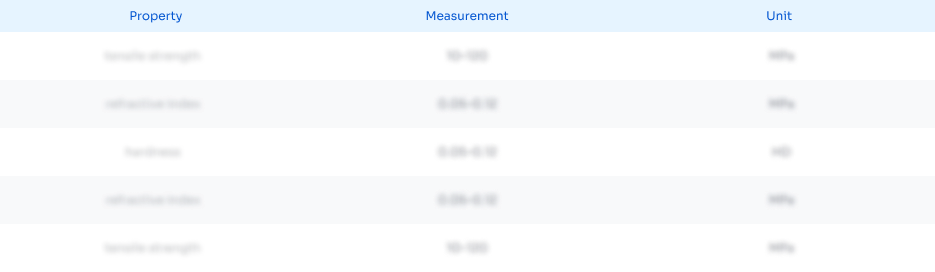
Abstract
Description
Claims
Application Information

- R&D Engineer
- R&D Manager
- IP Professional
- Industry Leading Data Capabilities
- Powerful AI technology
- Patent DNA Extraction
Browse by: Latest US Patents, China's latest patents, Technical Efficacy Thesaurus, Application Domain, Technology Topic, Popular Technical Reports.
© 2024 PatSnap. All rights reserved.Legal|Privacy policy|Modern Slavery Act Transparency Statement|Sitemap|About US| Contact US: help@patsnap.com