Double bond saturation and hydrodeoxygenation catalyst and its preparation method and application
A deoxygenation catalyst, molybdenum oxide technology, applied in chemical instruments and methods, physical/chemical process catalysts, fatty acid hydrogenation, etc., can solve the problems of olefin double bond not fully saturated deoxygenation rate, complex catalyst preparation procedure, general catalyst activity, etc. , to achieve the effect of good hydrothermal stability, favorable for scale-up and industrial production, and uniform dispersion of active metals
- Summary
- Abstract
- Description
- Claims
- Application Information
AI Technical Summary
Problems solved by technology
Method used
Examples
Embodiment 1
[0027] Mix 9.1g magnesium aluminum spinel, 0.6g praseodymium oxide, 9.1g strontium oxide, 17.3g aluminum oxide, 0.2g methylcellulose, 1.1g citric acid, 0.5g squash powder, and add to 37.9g deionized water Add 0.2g of nitric acid, then add 18.1g of alumina into deionized water, stir evenly, then knead with dry powder, extrude into a cylindrical shape, dry at 70°C for 8h, and roast at 500°C for 3h to obtain a shaped carrier.
[0028] The catalyst was prepared by an equal-volume co-impregnation method. 2.6g of basic nickel carbonate, 21.8g of molybdenum oxide, and 1.0g of ammonium phosphate were prepared as an aqueous solution, and the shaped carrier was immersed in the co-impregnation solution, aged for 10h, and dried at 95°C. After 10 hours, the catalyst was obtained by calcining at 450°C for 3.5 hours.
[0029]Pack 10.0ml of catalyst in a continuous flow fixed-bed reactor, vulcanize at 300°C for 5h, control the reaction temperature at 280°C, reaction pressure at 2.0MPa, reac...
Embodiment 2
[0031] Mix 4.5g magnesium aluminum spinel, 2.7g praseodymium oxide, 0.5g strontium oxide, 65.3g aluminum oxide, 3.7g methyl cellulose, 0.7g citric acid, 2.6g squash powder, and add to 70.6g deionized water Add 2.4g of nitric acid, then add 5.4g of alumina into deionized water, stir evenly, then knead with dry powder, extrude into a clover shape, dry at 80°C for 7h, and roast at 550°C for 3h to obtain a shaped carrier.
[0032] The catalyst was prepared by an equal volume co-impregnation method. 38.1g of nickel nitrate, 5.6g of ammonium tetramolybdate, and 7.8g of phosphoric acid were prepared as an aqueous solution, and the shaped carrier was immersed in the co-impregnation solution, aged for 12 hours, and dried at 100°C for 7 hours. , The catalyst was obtained by calcining at 500°C for 3h.
[0033] Pack 10.0ml of catalyst into a continuous flow fixed-bed reactor, vulcanize at 300°C for 5h, control the reaction temperature at 360°C, reaction pressure at 6.0MPa, reaction hydrog...
Embodiment 3
[0035] Mix 4.2g magnesium aluminum spinel, 0.4g praseodymium oxide, 0.8g strontium oxide, 16.8g aluminum oxide, 0.2g methyl cellulose, 0.3g citric acid, 0.4g squash powder, and add to 20.9g deionized water Add 0.2g of nitric acid, then add 5.6g of alumina into deionized water, stir evenly, then knead with dry powder, extrude into a clover shape, dry at 90°C for 8h, and roast at 600°C for 4h to obtain a shaped carrier.
[0036] The catalyst was prepared by the equal volume co-impregnation method. 4.0g nickel acetate, 3.8g ammonium heptamolybdate, and 0.5g phosphoric acid were prepared as an aqueous solution, and the shaped carrier was immersed in the co-impregnation solution, aged for 15h, and dried at 110°C for 6h , The catalyst was obtained by calcining at 550°C for 3h.
[0037] Fill 10.0ml of catalyst in a continuous flow fixed bed reactor, vulcanize at 300°C for 5h, control the reaction temperature at 380°C, reaction pressure at 4.0MPa, reaction hydrogen-oil ratio 800:1, re...
PUM
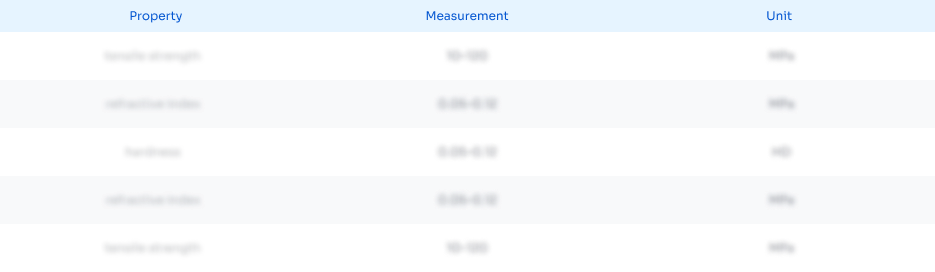
Abstract
Description
Claims
Application Information

- R&D Engineer
- R&D Manager
- IP Professional
- Industry Leading Data Capabilities
- Powerful AI technology
- Patent DNA Extraction
Browse by: Latest US Patents, China's latest patents, Technical Efficacy Thesaurus, Application Domain, Technology Topic, Popular Technical Reports.
© 2024 PatSnap. All rights reserved.Legal|Privacy policy|Modern Slavery Act Transparency Statement|Sitemap|About US| Contact US: help@patsnap.com