Non-contact eddy current sensor structure modal test method
A technology of eddy current sensors and eddy current sensors, which is applied in the testing of machines/structural components, testing of mechanical components, instruments, etc., can solve problems such as structural resonance and system damping reduction, and achieve high accuracy, stable test results, and time-consuming short effect
- Summary
- Abstract
- Description
- Claims
- Application Information
AI Technical Summary
Problems solved by technology
Method used
Image
Examples
Embodiment Construction
[0025] The present invention will be further described below in conjunction with the accompanying drawings and embodiments.
[0026] Such as figure 1 As shown, a structural modal test method of a steam turbine eddy current sensor, which uses the test environment stimulus response and pulse stimulus response to test the natural frequency and damping of the steam turbine eddy current sensor, specifically includes the following steps:
[0027] (1) In the cranking state of the unit, test its environmental vibration response through the online eddy current sensor, and calculate the response frequency f near the working speed according to the frequency response analysis 1 , f 2 , to preliminarily judge the vibration characteristics of the eddy current sensor. where f 1 , f 2 are the two response frequencies closest to the operating speed.
[0028] (2) Along the direction perpendicular to the metal casing of the eddy current sensor (such as figure 2 Shown) Hammer the shell of ...
PUM
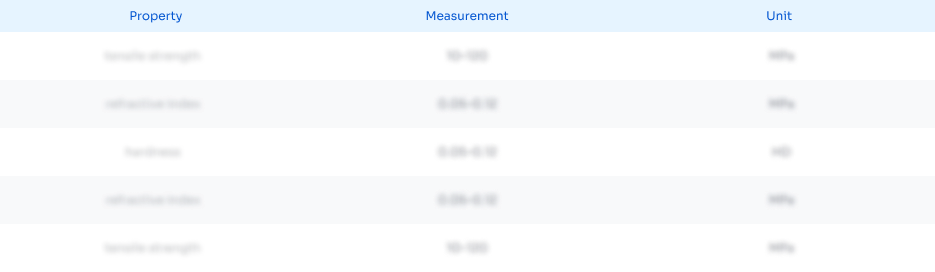
Abstract
Description
Claims
Application Information

- Generate Ideas
- Intellectual Property
- Life Sciences
- Materials
- Tech Scout
- Unparalleled Data Quality
- Higher Quality Content
- 60% Fewer Hallucinations
Browse by: Latest US Patents, China's latest patents, Technical Efficacy Thesaurus, Application Domain, Technology Topic, Popular Technical Reports.
© 2025 PatSnap. All rights reserved.Legal|Privacy policy|Modern Slavery Act Transparency Statement|Sitemap|About US| Contact US: help@patsnap.com