Feeding robot
A feeding robot and manipulator technology, applied in the field of parts processing, can solve problems such as low practicability and narrowing of use range
- Summary
- Abstract
- Description
- Claims
- Application Information
AI Technical Summary
Problems solved by technology
Method used
Image
Examples
Embodiment Construction
[0036] In order to enable those skilled in the art to better understand the technical solutions of the present invention, the present invention will be described in detail below in conjunction with the accompanying drawings and specific embodiments.
[0037] Such as figure 1 with figure 2 As shown, the embodiment of the present invention discloses a feeding robot for transporting workpieces, including: a base 6 , a slewing support 2 , a first arm 3 , a second arm 4 , a manipulator 1 and a controller 10 . The slewing support 2 is mounted on the base 6 and driven by a rotary motor 9 to rotate in a horizontal plane; the first arm 3 is mounted on the slewing support 2 and driven by a first motor to rotate in a vertical plane The second arm 4 is pivotally connected to the first arm 3, and is driven by a second motor to rotate in a vertical plane; the manipulator 1 is installed on the second arm 4 through the mounting body 5, and the manipulator 1 is used for Clamp the workpiece;...
PUM
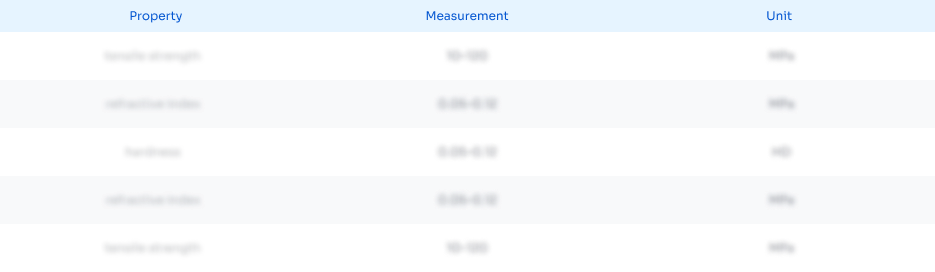
Abstract
Description
Claims
Application Information

- R&D
- Intellectual Property
- Life Sciences
- Materials
- Tech Scout
- Unparalleled Data Quality
- Higher Quality Content
- 60% Fewer Hallucinations
Browse by: Latest US Patents, China's latest patents, Technical Efficacy Thesaurus, Application Domain, Technology Topic, Popular Technical Reports.
© 2025 PatSnap. All rights reserved.Legal|Privacy policy|Modern Slavery Act Transparency Statement|Sitemap|About US| Contact US: help@patsnap.com