A kind of production method of potassium nitrate for optical glass
A production method and technology of optical glass, applied in chemical instruments and methods, preparation of alkali metal nitrates, alkali metal nitrates, etc., can solve the problems of less addition, many sources of impurities, uneconomical, etc. Residues, simple preparation process and reduced product quality
- Summary
- Abstract
- Description
- Claims
- Application Information
AI Technical Summary
Problems solved by technology
Method used
Image
Examples
Embodiment 1
[0020] In the method of the present invention, the processes or process steps of cooling crystallization, KNO3 crystal washing, filtering and dehydration and drying of finished products can be corresponding prior art.
[0021] The relevant process of this embodiment can be carried out according to the existing production process steps or the following process steps: raw material configuration, cooling and crystallization, KNO3 crystal washing, thermal melting and rebonding, filtration and dehydration and drying of finished products in sequence.
[0022] The raw material configuration includes: the raw material potassium chloride and ammonium nitrate and water or process circulating water are configured according to a certain ratio, that is, the ratio of the existing production process, heated, and reacted at a temperature of 80-110°C to form a potassium nitrate reaction solution. Controlling the Cl in the reaction solution — and NH4 + Concentrations were 16-22%, 7-12%, respe...
Embodiment 2
[0028] In this example, its thermal melting recombination includes: adding potassium and sodium compound salts to the supersaturated solution of KNO3 semi-finished crystals, and then according to its Cl — and NH4 + The content of potassium and sodium compound salt is added according to the proportion, and the main impurity NH4 in potassium nitrate is + Ammonia gas is generated through the reaction to remove; at the same time, according to the chemical characteristics of sodium chloride high temperature reverse precipitation, by controlling the corresponding temperature of the solution, the chloride radicals in it react with sodium ions to form sodium chloride, thereby eliminating chloride ions and obtaining impurity-removed High-purity potassium nitrate supersaturated solution; thereby achieving the purpose of improving product purity.
Embodiment 3
[0030] In the thermal melting rebonding process of the present invention, a mixture of silicic acid and potassium metaaluminate (or mixed solution) is added to the supersaturated solution of KNO3 semi-finished crystals, and the ratio of silicic acid to potassium metaaluminate is 1:1. The remaining process methods and the like can be similar to any of the above-mentioned embodiments.
[0031] In the technical scheme of the production method of potassium nitrate for optical glass of the present invention, the potassium chloride emulsion after emulsification is water-soluble potassium chloride. Its potassium sodium compound salt can be the compound salt of sodium carbonate and potassium carbonate. The remaining modes and corresponding material proportions of this example can be similar to those of the above-mentioned embodiment.
PUM
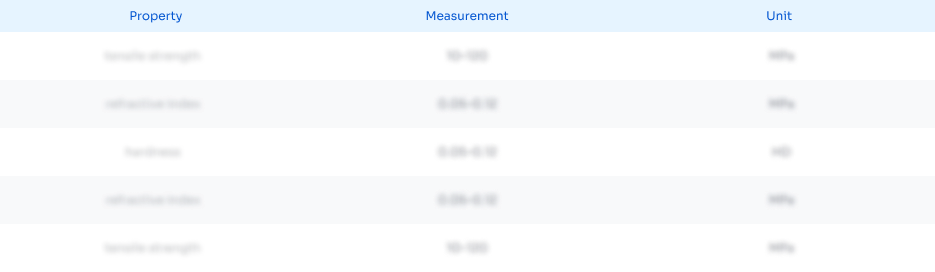
Abstract
Description
Claims
Application Information

- Generate Ideas
- Intellectual Property
- Life Sciences
- Materials
- Tech Scout
- Unparalleled Data Quality
- Higher Quality Content
- 60% Fewer Hallucinations
Browse by: Latest US Patents, China's latest patents, Technical Efficacy Thesaurus, Application Domain, Technology Topic, Popular Technical Reports.
© 2025 PatSnap. All rights reserved.Legal|Privacy policy|Modern Slavery Act Transparency Statement|Sitemap|About US| Contact US: help@patsnap.com