Visual RTM mould capable of infinitely adjusting thickness of composite plate
A composite material board, stepless adjustment technology, applied in the field of composite material product molding, can solve problems such as affecting the quality of sheet material products, difficult to ensure sealing, and achieve the goal of reducing product defects, easy mold opening, and optimizing mold filling flow channels. Effect
- Summary
- Abstract
- Description
- Claims
- Application Information
AI Technical Summary
Problems solved by technology
Method used
Image
Examples
Embodiment 1
[0050] The invention provides a visual RTM mold capable of steplessly adjusting the thickness of the composite material sheet, the structure of which is as follows Figure 1 to Figure 6 shown, including:
[0051] Roller 1, frame 2, pouring device 3, upper template 4, lower template 5, gas spring 6, mold opening mechanism 7, cavity adjustment mechanism 8 and heating component 9.
[0052] Frame 2 is used to carry the weight of the entire RTM mold and fix the relevant parts of the RTM mold. In order to facilitate the movement, the bottom is provided with rollers 1 .
[0053] One end of the upper template 4 is connected with the frame 2 through a hinge, and the side of the upper template 4 is connected with the frame 2 by a gas spring 6 . During the push-out process of the gas spring 6, the upper template 4 opens upwards around the hinge. On the contrary, during the retraction process of the gas spring 6, the upper formwork 4 moves toward the lower formwork 5 around the hinge. ...
PUM
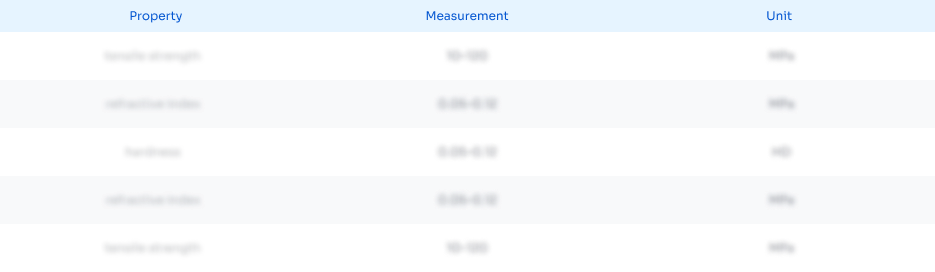
Abstract
Description
Claims
Application Information

- R&D Engineer
- R&D Manager
- IP Professional
- Industry Leading Data Capabilities
- Powerful AI technology
- Patent DNA Extraction
Browse by: Latest US Patents, China's latest patents, Technical Efficacy Thesaurus, Application Domain, Technology Topic, Popular Technical Reports.
© 2024 PatSnap. All rights reserved.Legal|Privacy policy|Modern Slavery Act Transparency Statement|Sitemap|About US| Contact US: help@patsnap.com