3D machine visual forklift travelling auxiliary safety system and method
An auxiliary safety and machine vision technology, applied in the direction of lifting equipment safety devices, vehicle parts, lifting devices, etc., can solve problems such as hidden dangers, poor detection stability, poor recognition accuracy, etc., to prevent accidents, improve safety, Stable running effect
- Summary
- Abstract
- Description
- Claims
- Application Information
AI Technical Summary
Problems solved by technology
Method used
Image
Examples
Embodiment Construction
[0028] Specific embodiments of the present invention will be further described in detail below in conjunction with the accompanying drawings.
[0029] like figure 1 As shown, a 3D machine vision forklift driving auxiliary safety system includes a work environment perception subsystem 1.1, a vehicle state monitoring subsystem 1.2, a control output subsystem 1.3 and an information processing subsystem 1.4, the work environment perception subsystem 1.1, The vehicle state monitoring subsystem 1.2 and the control output subsystem 1.3 are connected to the information processing subsystem 1.4 through a communication network or input and output modules; the operating environment perception subsystem 1.1 includes a front intelligent depth camera 1.5, a side intelligent depth camera 1.6, a rear The intelligent depth camera 1.7, the side collision switch 1.8 and the rear collision switch 1.9 are used to collect various information around the forklift operation to ensure the safe driving ...
PUM
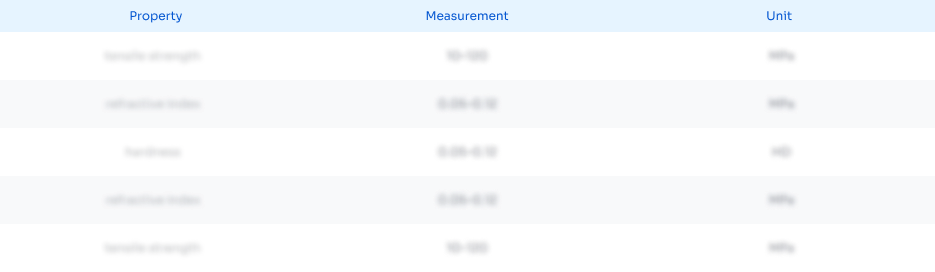
Abstract
Description
Claims
Application Information

- R&D
- Intellectual Property
- Life Sciences
- Materials
- Tech Scout
- Unparalleled Data Quality
- Higher Quality Content
- 60% Fewer Hallucinations
Browse by: Latest US Patents, China's latest patents, Technical Efficacy Thesaurus, Application Domain, Technology Topic, Popular Technical Reports.
© 2025 PatSnap. All rights reserved.Legal|Privacy policy|Modern Slavery Act Transparency Statement|Sitemap|About US| Contact US: help@patsnap.com