Method and Vibration Damping Device for Adjusting Gas Seal Gap of Steam Turbine with Air Jet Vibration Damping
A steam turbine and steam turbine blade technology, applied in mechanical equipment, engine components, machines/engines, etc., to reduce steam leakage, reduce radial runout, and maintain stability
- Summary
- Abstract
- Description
- Claims
- Application Information
AI Technical Summary
Problems solved by technology
Method used
Image
Examples
specific Embodiment approach 1
[0041] Specific implementation mode one: the following combination Figure 6 to Figure 9 This embodiment will be specifically described. The method for adjusting the gas seal gap of the steam turbine by the air injection damping is realized through the following steps:
[0042] Step 1: start the steam turbine; before starting, the gap t between the surface of the inner hole of the air seal assembly at the top of the moving blade of the steam turbine and the outer surface of the blade of the steam turbine is between 1.5 and 10 mm;
[0043] Step 2. After the steam turbine reaches the normal speed, adjust the centralizer assembly installed at the inner hole of the diaphragm, so that the upper bearing bush 9-1 and the lower bearing bush 9-2 on the centralizer assembly tend to close gradually and surround the main shaft 9-3 of the steam turbine , to reduce the radial runout of the steam turbine main shaft 9-3; in the initial state, the distance between the inner surface of the upp...
specific Embodiment approach 2
[0048] Specific implementation mode two: the following combination Figure 6 and Figure 8 This embodiment will be specifically described. This embodiment is compared with Embodiment 1: this method also includes two groups of distance sensors 6-14 and a group of vibration sensors 8-1, and the first group of distance sensors 6-14 is arranged on the air seal body 6-11 to Real-time measurement of the gap between the gas seal body 6-11 and the outer surface of the steam turbine blade 6-12 and the radial runout of the outer surface of the steam turbine blade 6-12; the second group of distance sensors 6-14 are arranged on the upper bearing bush 9-1 and the lower On the bearing bush 9-2, to measure the gap between the upper bearing bush 9-1 and the lower bearing bush 9-2 and the steam turbine main shaft 9-3 and the radial runout of the steam turbine main shaft 9-3 in real time; a set of vibration sensors 8-1 is arranged on the upper bearing bush 9-1 and the back side of the lower b...
specific Embodiment approach 3
[0051] Specific implementation mode three: the following combination Figure 8 This embodiment will be specifically described. The third step also includes the following technical means, in the process of making the surface of the inner hole of the air seal assembly at the top of the moving blade close to the outer surface of the steam turbine blade 6-12, the gap between the air seal body and the outer surface of the steam turbine blade 6-12 is collected in real time 1. The radial runout of the outer surface of the steam turbine blade 6-12 and the vibration data collected by the vibration sensor 8-1 to ensure that the value of the gap is always greater than the value of the radial runout. If the vibration data increases abnormally, it will immediately reverse the action to increase The distance between the surface of the inner hole of the air seal assembly at the top of the large moving blade and the outer surface of the steam turbine blade 6-12, when the vibration data return...
PUM
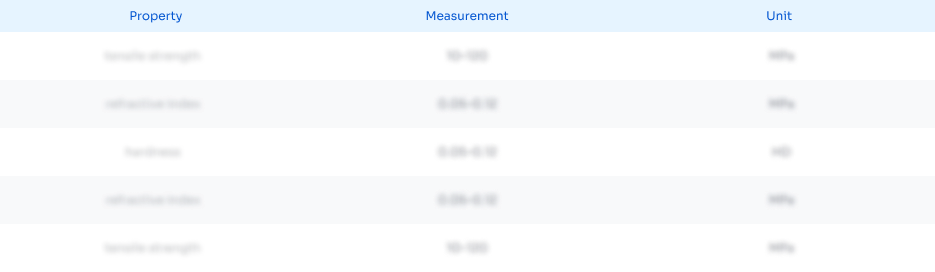
Abstract
Description
Claims
Application Information

- R&D
- Intellectual Property
- Life Sciences
- Materials
- Tech Scout
- Unparalleled Data Quality
- Higher Quality Content
- 60% Fewer Hallucinations
Browse by: Latest US Patents, China's latest patents, Technical Efficacy Thesaurus, Application Domain, Technology Topic, Popular Technical Reports.
© 2025 PatSnap. All rights reserved.Legal|Privacy policy|Modern Slavery Act Transparency Statement|Sitemap|About US| Contact US: help@patsnap.com