A three-degree-of-freedom parallel mechanism with two rotations and one displacement with few joints
A technology of degrees of freedom and joints, applied in the field of robotics, can solve problems such as difficult control, large number of single-degree-of-freedom joints, complex kinematic equations, etc., to achieve the effects of strong practicability, high structural rigidity, and simple control model.
- Summary
- Abstract
- Description
- Claims
- Application Information
AI Technical Summary
Problems solved by technology
Method used
Image
Examples
Embodiment 1
[0009] exist figure 1 In the schematic diagram of the two-rotation-one-movement parallel mechanism with few joints shown, one end of the first upper link 4 of the first branch chain is connected to the moving platform 2 through the second rotating pair 3, and the other end of the first upper link is connected through the second A moving pair 5 is connected with one end of the first lower link 6, and the other end of the first lower link is connected with the fixed platform 1 through the first rotating pair 7; one end of the second upper link 9 of the second branch chain passes through The first Hooke hinge 8 is connected with the moving platform, the other end of the second upper link is connected with one end of the second lower link 11 through the second moving pair 10, and the other end of the second lower link is connected by the third rotation The pair 12 is connected with the fixed platform; one end of the third upper link 14 of the third branch chain is connected with t...
Embodiment 2
[0011] Such as figure 2 As shown, one end of the first upper link 4 of the first branch chain is connected to the moving platform 2 through the second rotating pair 3, and the other end of the first upper link is connected to the first lower link 6 through the first moving pair 5. One end of the first lower link is connected with the fixed platform 1 through the first rotating pair 7; one end of the second upper link 9 of the second branch is connected with the moving platform through the first Hooke hinge 8, The other end of the second upper link is connected with an end of the second lower link 11 through the fifth rotary pair 18, and the other end of the second lower link is connected with the fixed platform through the third rotary pair 12; the third branch chain One end of the third upper connecting rod 14 is connected with the moving platform through the fourth rotating pair 13, and the other end of the third upper connecting rod is connected with one end of the third l...
PUM
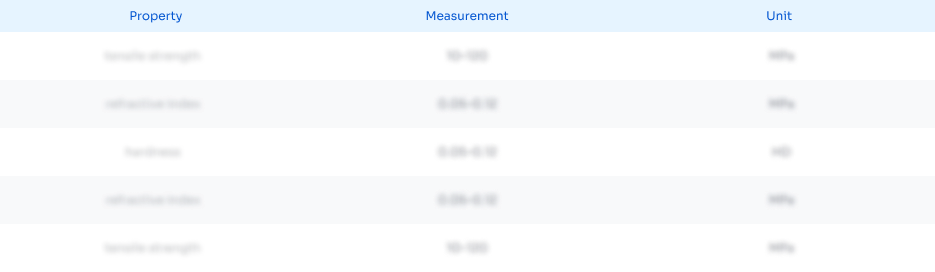
Abstract
Description
Claims
Application Information

- Generate Ideas
- Intellectual Property
- Life Sciences
- Materials
- Tech Scout
- Unparalleled Data Quality
- Higher Quality Content
- 60% Fewer Hallucinations
Browse by: Latest US Patents, China's latest patents, Technical Efficacy Thesaurus, Application Domain, Technology Topic, Popular Technical Reports.
© 2025 PatSnap. All rights reserved.Legal|Privacy policy|Modern Slavery Act Transparency Statement|Sitemap|About US| Contact US: help@patsnap.com