A Modular Joint of Manipulator without Torque Sensor
A modular joint and sensor technology, applied in the field of robots, can solve the problems of complex transmission structure, large joint weight and volume, increase joint weight and volume, etc., and achieve the effect of simple transmission structure, reducing joint mass and shortening length.
- Summary
- Abstract
- Description
- Claims
- Application Information
AI Technical Summary
Problems solved by technology
Method used
Image
Examples
Embodiment Construction
[0018] refer to figure 1 , a modular joint of a mechanical arm without a moment sensor of the present invention includes a housing 1, a rear cover 19 fixedly connected to the housing, a braking mechanism, a transmission mechanism, and a transmission mechanism connected to the housing 1. Output shaft 2 and control mechanism.
[0019] The transmission mechanism includes a rotating shaft 3, a motor 7 arranged on the rotating shaft 3, a harmonic reducer 5 rigidly connected to one end of the rotating shaft 3, a first adapter 4 rigidly connected to the other end of the rotating shaft 3, and a harmonic reducer 5. Rigidly connected second adapter 6. Further, the positioning of the motor 7 is realized by the following structure: the motor 7 includes a rotor 7-1 fitted on the rotating shaft 3 and a stator 7-2 arranged on the periphery of the rotor 7-1, and the stator 7-2 is fitted with a The stator sleeve 9 positioned in the circumferential direction of the motor 7, the rotating shaft...
PUM
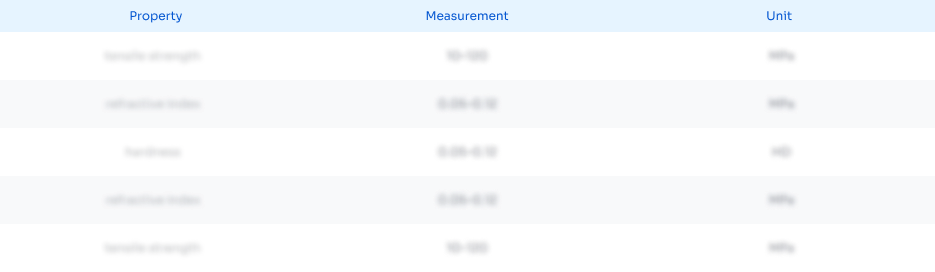
Abstract
Description
Claims
Application Information

- R&D
- Intellectual Property
- Life Sciences
- Materials
- Tech Scout
- Unparalleled Data Quality
- Higher Quality Content
- 60% Fewer Hallucinations
Browse by: Latest US Patents, China's latest patents, Technical Efficacy Thesaurus, Application Domain, Technology Topic, Popular Technical Reports.
© 2025 PatSnap. All rights reserved.Legal|Privacy policy|Modern Slavery Act Transparency Statement|Sitemap|About US| Contact US: help@patsnap.com