Energy-saving method for boiler waste heat recovery
A waste heat recovery and boiler waste heat technology, which is applied in the field of boiler waste heat recovery, can solve the problems of waste heat waste, high exhaust gas temperature, waste of fuel, etc., and achieve high waste heat recovery effect, improved economic benefits, and convenient use
- Summary
- Abstract
- Description
- Claims
- Application Information
AI Technical Summary
Problems solved by technology
Method used
Examples
Embodiment 1
[0018] A method for boiler waste heat recovery and energy saving, comprising the following steps:
[0019] S1. Separation of flue: 3 main flues and 1 spare flue are arranged on the flue outlet of the boiler, and each spare flue is opened and closed by a solenoid valve;
[0020] S2. Set up waste heat recoverers: 2 graded waste heat recoverers are installed in turn on each main flue and each spare flue, and each graded waste heat recoverers are connected by water pipes, using water as the medium for waste heat The recovery of waste heat, each main flue and each spare flue is equipped with a three-stage waste heat recovery device;
[0021] S3. Control the communication between each waste heat recovery device: each graded waste heat recovery device is equipped with a solenoid valve connected to the water pipe, and the second-level waste heat recovery device and the second-level waste heat recovery device are equipped with temperature sensors. And the temperature difference betwee...
Embodiment 2
[0025] A method for boiler waste heat recovery and energy saving, comprising the following steps:
[0026] S1. Separation of flue: 4 main flues and 2 spare flues are arranged on the smoke outlet of the boiler, and each spare flue is opened and closed by a solenoid valve;
[0027] S2. Set up waste heat recoverers: 3 graded waste heat recoverers are arranged in turn on each main flue and each spare flue, and each graded waste heat recoverers are connected by water pipes, using water as the medium for waste heat The recovery of waste heat, each main flue and each spare flue is equipped with a three-stage waste heat recovery device;
[0028] S3. Control the communication between each waste heat recovery device: each graded waste heat recovery device is equipped with a solenoid valve connected to the water pipe, and the second-level waste heat recovery device and the second-level waste heat recovery device are equipped with temperature sensors. And the temperature difference betwe...
Embodiment 3
[0032] A method for boiler waste heat recovery and energy saving, comprising the following steps:
[0033] S1. Separation of flue: 5 main flues and 3 spare flues are arranged on the smoke outlet of the boiler, and each spare flue is opened and closed by a solenoid valve;
[0034] S2. Set up waste heat recoverers: 5 graded waste heat recoverers are arranged in turn on each main flue and each standby flue, and each graded waste heat recoverers are connected by water pipes, using water as the medium for waste heat The recovery of waste heat, each main flue and each spare flue is equipped with a three-stage waste heat recovery device;
[0035] S3. Control the communication between each waste heat recovery device: each graded waste heat recovery device is equipped with a solenoid valve connected to the water pipe, and the second-level waste heat recovery device and the second-level waste heat recovery device are equipped with temperature sensors. And the temperature difference bet...
PUM
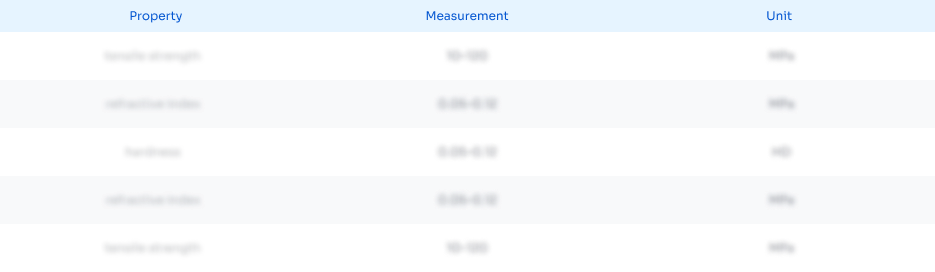
Abstract
Description
Claims
Application Information

- R&D
- Intellectual Property
- Life Sciences
- Materials
- Tech Scout
- Unparalleled Data Quality
- Higher Quality Content
- 60% Fewer Hallucinations
Browse by: Latest US Patents, China's latest patents, Technical Efficacy Thesaurus, Application Domain, Technology Topic, Popular Technical Reports.
© 2025 PatSnap. All rights reserved.Legal|Privacy policy|Modern Slavery Act Transparency Statement|Sitemap|About US| Contact US: help@patsnap.com