Stand column welding tool
A welding tool and column technology, applied in welding equipment, auxiliary welding equipment, welding/cutting auxiliary equipment, etc., can solve the problems of low efficiency, excessive flange assembly gap, low production efficiency, etc., to improve work efficiency, Guaranteed installation accuracy
- Summary
- Abstract
- Description
- Claims
- Application Information
AI Technical Summary
Problems solved by technology
Method used
Image
Examples
Embodiment Construction
[0034] In order to make the technical problems solved by the present invention, the technical solutions adopted and the technical effects achieved clearer, the present invention will be further described in detail below in conjunction with the accompanying drawings and embodiments. It should be understood that the specific embodiments described here are only used to explain the present invention, but not to limit the present invention.
[0035] refer to Figure 1-2 , the invention discloses a column welding tool, comprising: a stand 13, a fixed seat 1, a movable seat, a support seat 12, and a pressing mechanism;
[0036] A fixed seat 1 is installed at one end of the stand 13, and a movable seat is installed at the other end;
[0037] refer to Figure 3-4 , the fixed seat 1 includes: a fixed sleeve and a seat body installed up and down, and a positioning disc 2 is vertically installed on the mounting surface of the fixed sleeve;
[0038] refer to Figure 5-6 , the movable s...
PUM
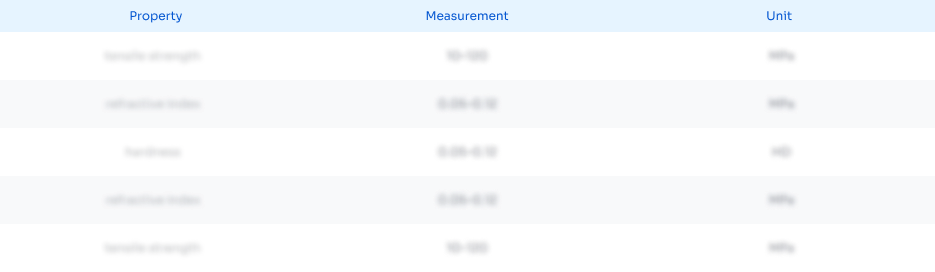
Abstract
Description
Claims
Application Information

- Generate Ideas
- Intellectual Property
- Life Sciences
- Materials
- Tech Scout
- Unparalleled Data Quality
- Higher Quality Content
- 60% Fewer Hallucinations
Browse by: Latest US Patents, China's latest patents, Technical Efficacy Thesaurus, Application Domain, Technology Topic, Popular Technical Reports.
© 2025 PatSnap. All rights reserved.Legal|Privacy policy|Modern Slavery Act Transparency Statement|Sitemap|About US| Contact US: help@patsnap.com