Filter for casting and filtering system comprising same
A filtering system and filter technology, applied in casting molding equipment, molds, mold components, etc., can solve the problems of increasing the horizontal projection area of the gating system, increasing the sand intake of the gating system, and a single structure of the filtering system, and reducing the The effect of sand intake, increased sand intake, and flexible structure
- Summary
- Abstract
- Description
- Claims
- Application Information
AI Technical Summary
Problems solved by technology
Method used
Image
Examples
Embodiment 1
[0044] figure 1 The shown single filter has a structure including: an inlet (101) arranged on the top of the filter for introducing molten iron into the filter and connecting to the runner in the gating system; The upper liquid storage area (102) and the lower liquid storage area (103) are arranged below the port (101) and are mirrored along the horizontal axis to reduce the flow rate of molten iron and enlarge the contact area between molten iron and the filter screen; The middle of the liquid area (102) and the lower liquid storage area (103), the cross section is a rectangle, the boundary size is larger than the cross-sectional size of the liquid storage area, and is used to carry the filter screen tank (104); The side surface in the width direction of the filter mesh slot (104), the longitudinal section size is larger than the longitudinal section size of the filter mesh slot (104), the window (105) for inserting the filter mesh into the filter mesh slot (104), and the win...
Embodiment 2
[0047] figure 2The shown in-line filtration system has a structure including: a main inlet (201) arranged at the top for introducing molten iron into the filtration system and connecting to the sprue of the gating system; 201) below, extending distribution to reduce the flow rate of molten iron and distributing molten iron to each filter (100) deceleration flow channel (202), there is only one deceleration flow channel (202), horizontally extending distribution; arranged in the main inlet The flow port (201) is directly below the first end of the deceleration flow channel, and is located below the deceleration flow channel (202), for reducing the flow rate of molten iron and collecting the first strand of iron charged into the filter system A buffer pocket (203) for liquid; four filters (100) arranged in parallel under the deceleration flow channel (202); located at the second end of the deceleration flow channel (202), used to clean the loose sand in the filter system a mai...
Embodiment 3
[0050] image 3 The shown rotary filtration system has a structure including: a main inlet (201) arranged at the top for introducing molten iron into the filtration system and connected to the sprue of the gating system; Below 201), there are deceleration flow channels (202) for reducing the flow rate of molten iron and distributing molten iron to each filter (100). The inner circumferential array is distributed; it is arranged directly below the main inlet (201), communicates with the first end of the deceleration flow channel, and is located below the deceleration flow channel (202), so as to reduce the flow rate of molten iron and a buffer socket (203) for collecting the first strand of molten iron charged into the filtration system; a filter (100) is connected below each deceleration flow channel (202); hanging handles (206) symmetrically distributed on both sides of the end .
[0051] This rotary filter system is usually used in the production of rotary castings with ce...
PUM
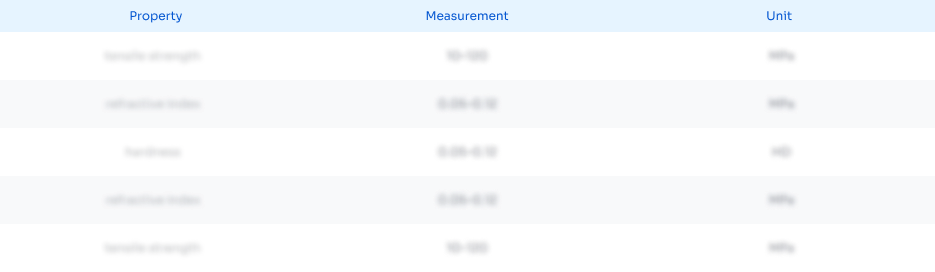
Abstract
Description
Claims
Application Information

- R&D
- Intellectual Property
- Life Sciences
- Materials
- Tech Scout
- Unparalleled Data Quality
- Higher Quality Content
- 60% Fewer Hallucinations
Browse by: Latest US Patents, China's latest patents, Technical Efficacy Thesaurus, Application Domain, Technology Topic, Popular Technical Reports.
© 2025 PatSnap. All rights reserved.Legal|Privacy policy|Modern Slavery Act Transparency Statement|Sitemap|About US| Contact US: help@patsnap.com