Low-damage processing method of film holes in single crystal high-pressure-turbine hollow blade of aircraft engine
An aero-engine, hollow blade technology, applied in metal processing equipment, manufacturing tools, welding equipment and other directions, can solve the problem that the fatigue life of parts cannot be well guaranteed, avoid recrystallization, prevent damage to the wall, improve The effect of surface integrity
- Summary
- Abstract
- Description
- Claims
- Application Information
AI Technical Summary
Problems solved by technology
Method used
Image
Examples
Embodiment 1
[0056] Parts: a single crystal high-vortex hollow blade of an aero-engine;
[0057] Before processing the air film holes, use absorbent cotton dipped in absolute alcohol to carefully wipe the surface of the blade, including the leaf pot, leaf back, tenon and other areas, to ensure that the area to be processed is completely covered, and then put the cleaned blade into a 70°C drying oven for drying Dry for 30min.
[0058] During this period, adjust the clamping state of the fixture and the blade to ensure the relative coordinates between the machine tool and the origin of the blade. Lock the clamp and blade at the same time.
[0059] Before the laser gas film hole, through the three-dimensional scanning auxiliary positioning module, the blade is scanned in all directions, and the estimated time is 10 minutes. Afterwards, point cloud processing is performed on the data points obtained after scanning to form hole position coordinate point data and generate a coordinate file, wh...
PUM
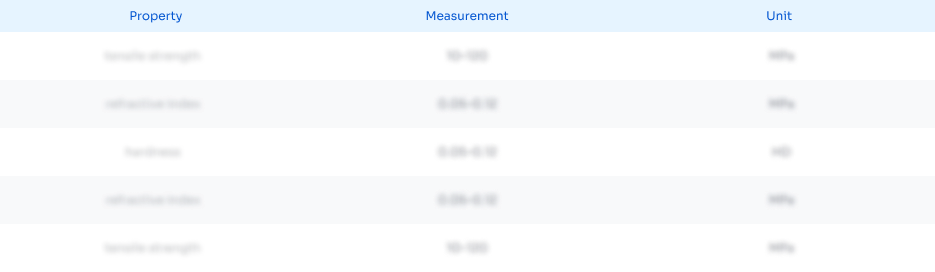
Abstract
Description
Claims
Application Information

- R&D
- Intellectual Property
- Life Sciences
- Materials
- Tech Scout
- Unparalleled Data Quality
- Higher Quality Content
- 60% Fewer Hallucinations
Browse by: Latest US Patents, China's latest patents, Technical Efficacy Thesaurus, Application Domain, Technology Topic, Popular Technical Reports.
© 2025 PatSnap. All rights reserved.Legal|Privacy policy|Modern Slavery Act Transparency Statement|Sitemap|About US| Contact US: help@patsnap.com