Thermal virtual experiment method
A technology of virtual test and physical test, which is applied in the field of thermal virtual test, can solve the problems that the thermal virtual test method has not been reported yet, and achieve the effect of shortening the development cycle, reducing the number of physical tests, and improving development efficiency
- Summary
- Abstract
- Description
- Claims
- Application Information
AI Technical Summary
Benefits of technology
Problems solved by technology
Method used
Examples
Embodiment Construction
[0016] The present invention will be described in further detail below by means of specific embodiments:
[0017] 1) Using the pneumatic heating module of HAJIF2013 software, HAJIF2013 software is a market product.
[0018] 2) Establish or import structural digital model
[0019] Product digital models can be CATIA, CAXA models, etc.
[0020] 3) Virtual analysis of thermal response under ideal conditions
[0021] Use the ASTSA or MSC Patran / Nastran thermal analysis software of the pneumatic heating module to analyze the thermal response of the product and obtain preliminary analysis results to guide the physical thermal test.
[0022] 4) Generate thermal virtual test scene
[0023] If the physical test is heated by a flat-plate heater, start the heat flow distribution calculation module of the flat-plate heater to design the flat-plate heater; if the physical test uses a cylindrical heater, start the cylindrical heater parametric design module to design the cylindrical heat...
PUM
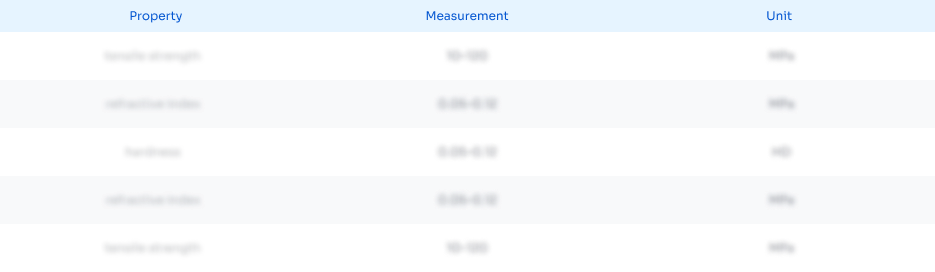
Abstract
Description
Claims
Application Information

- Generate Ideas
- Intellectual Property
- Life Sciences
- Materials
- Tech Scout
- Unparalleled Data Quality
- Higher Quality Content
- 60% Fewer Hallucinations
Browse by: Latest US Patents, China's latest patents, Technical Efficacy Thesaurus, Application Domain, Technology Topic, Popular Technical Reports.
© 2025 PatSnap. All rights reserved.Legal|Privacy policy|Modern Slavery Act Transparency Statement|Sitemap|About US| Contact US: help@patsnap.com