Fully-automatic shaping mechanism for welding joint of pressure water storage bucket
A water storage bucket, fully automatic technology, applied in turning equipment, turning equipment, metal processing and other directions, can solve the problems of low production efficiency, high labor intensity and high labor cost
- Summary
- Abstract
- Description
- Claims
- Application Information
AI Technical Summary
Problems solved by technology
Method used
Image
Examples
Embodiment Construction
[0020] The invention relates to a fully automatic seam shaping mechanism for a pressure water storage tank, such as figure 1 — Figure 8Shown, comprise frame 1, be provided with feeding device 2, positioning device 4, feeding device 5, trimming rotating device 6 and trimming shaping device 8 on the frame; Described feeding device 2 comprises feeding conveyor belt 21 And support 22, the pressure water storage tank 23 is set on the feeding conveyor belt, the air filling nozzle 24 is set under the pressure water storage tank, the support is fixed with the frame 1, the X-direction slide rail 26 is arranged on the support, and the X-direction slide rail is provided on the X-direction slide rail. Slider 27, the X-direction slider is driven by the X-direction moving cylinder 28, the Y-direction slide rail 29 is set on the X-direction slide rail, the Y-direction slide block 30 is arranged on the Y-direction slide rail, and the Y-direction slider moves through the Y-direction cylinder ...
PUM
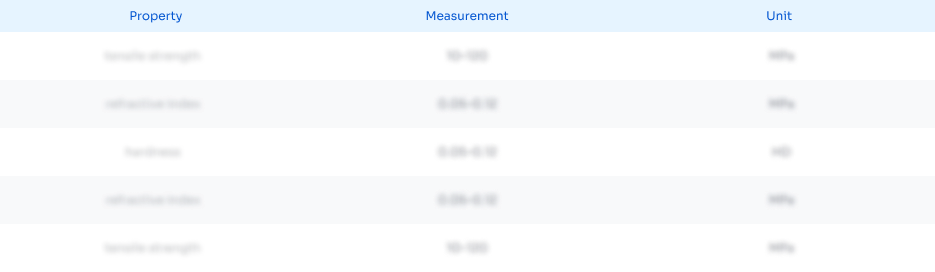
Abstract
Description
Claims
Application Information

- R&D Engineer
- R&D Manager
- IP Professional
- Industry Leading Data Capabilities
- Powerful AI technology
- Patent DNA Extraction
Browse by: Latest US Patents, China's latest patents, Technical Efficacy Thesaurus, Application Domain, Technology Topic, Popular Technical Reports.
© 2024 PatSnap. All rights reserved.Legal|Privacy policy|Modern Slavery Act Transparency Statement|Sitemap|About US| Contact US: help@patsnap.com